Groundbreaking construction projects are revolutionizing the industry through digital twin technology, modular innovation, and advanced procurement management strategies. From Dubai’s 3D-printed office buildings to Singapore’s forest-integrated skyscrapers, these developments showcase how emerging technologies and sustainable practices are reshaping our built environment.
Leading construction firms worldwide are integrating artificial intelligence for real-time project monitoring, implementing robotics for dangerous tasks, and utilizing smart materials that self-heal and adapt to environmental conditions. These innovations have reduced project timelines by up to 30% while improving safety metrics and environmental performance.
The transformation extends beyond technology to encompass new collaborative delivery models, where traditional contractor-client relationships evolve into integrated partnerships. Projects like Copenhagen’s Resource Rows demonstrate how circular economy principles can be embedded into construction processes, repurposing 75% of materials from demolished buildings to create sustainable housing solutions.
This surge in innovative construction approaches marks a decisive shift from conventional methods, promising enhanced efficiency, reduced environmental impact, and unprecedented architectural possibilities. Industry leaders who embrace these advancements position themselves at the forefront of construction’s evolution.
Digital-First Procurement Success Stories
The Copenhagen Smart City Project
Copenhagen’s smart city initiative showcases how innovative procurement strategies can drive sustainable urban development. Launched in 2014, the project revolutionized traditional construction procurement by implementing advanced digital procurement platforms integrated with IoT sensors and real-time data analytics.
The project’s procurement framework prioritizes three key elements: sustainability requirements, innovation partnerships, and circular economy principles. Contractors must demonstrate their ability to meet specific environmental targets, including a 40% reduction in carbon emissions compared to conventional construction methods. The municipality established a pre-qualification system that evaluates bidders based on their sustainable innovation capabilities and track record.
Notable achievements include the development of smart building systems that optimize energy consumption through predictive maintenance and automated controls. The procurement process encouraged collaboration between technology providers and construction firms, resulting in innovative solutions like modular green roofs and intelligent waste management systems.
The initiative’s success lies in its performance-based procurement model, where contractors are incentivized to exceed sustainability targets. This approach has led to a 25% reduction in construction waste and a 30% improvement in energy efficiency across new buildings. The Copenhagen model has since been adopted by other European cities, demonstrating how strategic procurement can accelerate sustainable urban development while maintaining cost-effectiveness.
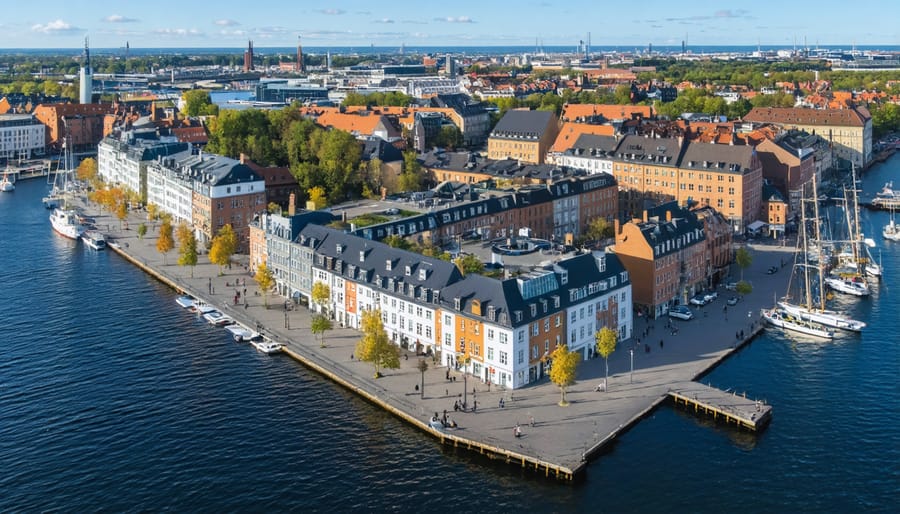
Sydney Metro’s Digital Supply Chain
Sydney Metro’s groundbreaking digital supply chain transformation has set new benchmarks for procurement efficiency in major infrastructure projects. The AU$50 billion initiative implemented a cloud-based digital procurement platform that connects over 5,000 suppliers and contractors across multiple project stages, streamlining traditionally complex processes.
The system’s innovative features include real-time inventory tracking, automated compliance monitoring, and predictive analytics for material demands. Project managers report a 30% reduction in procurement cycles and a 25% decrease in administrative costs since implementation. This digital ecosystem enables seamless collaboration between stakeholders, from designers to contractors and suppliers.
A standout feature is the platform’s integration with Building Information Modeling (BIM), allowing for precise material quantification and just-in-time delivery scheduling. The system’s artificial intelligence component analyzes historical data to optimize ordering patterns and predict potential supply chain disruptions.
The procurement strategy also incorporates sustainability metrics, tracking the carbon footprint of materials and transportation. Suppliers must meet strict environmental criteria, monitored through digital reporting tools. This approach has resulted in a 20% reduction in material waste and improved sustainability outcomes across the project.
The platform’s success has influenced other major infrastructure projects globally, with several international transport authorities now adopting similar digital procurement frameworks. The Sydney Metro case demonstrates how digital transformation can revolutionize construction supply chain management while supporting broader project objectives.
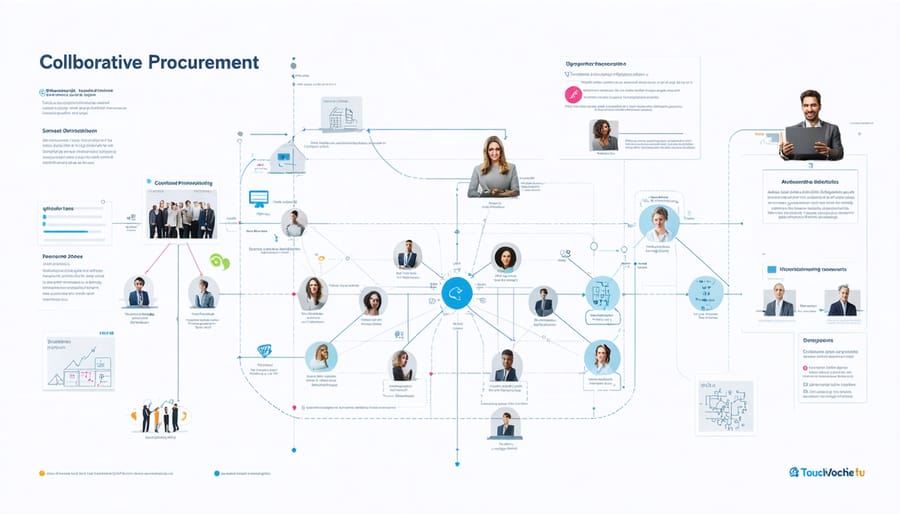
Collaborative Procurement Models
Early Contractor Involvement (ECI)
Early Contractor Involvement (ECI) has emerged as a game-changing procurement approach in innovative construction projects, delivering significant improvements in project outcomes through enhanced collaboration and early risk mitigation. This methodology, when implemented effectively, has demonstrated up to 15% cost savings and 20% faster project delivery times compared to traditional procurement methods.
Recent successful implementations include the Brisbane Cross River Rail project, where ECI enabled contractors to contribute valuable insights during the design phase, resulting in optimized construction methodologies and reduced environmental impact. The contractor’s early input led to innovative solutions for tunnel boring and station construction, ultimately saving AUD 200 million in project costs.
The effectiveness of ECI lies in its ability to align project stakeholders’ interests from the outset. By involving contractors during the pre-construction phase, teams can identify potential challenges, optimize designs for constructability, and develop more accurate cost estimates. This collaborative approach has proven particularly valuable in complex infrastructure projects where traditional procurement methods often struggle to address unforeseen challenges.
Key success factors for ECI implementation include:
– Clear definition of roles and responsibilities
– Transparent risk allocation and pricing mechanisms
– Early establishment of integrated project teams
– Regular workshops and communication protocols
– Shared project objectives and KPIs
However, organizations must carefully consider project suitability for ECI adoption. The approach requires significant resource commitment from all parties and works best in projects with high complexity, technical challenges, or significant risk profiles. The Swedish Transport Administration’s implementation of ECI in their railway infrastructure projects demonstrates how careful selection criteria and structured implementation can lead to successful outcomes.
Alliance Contracting Success
Alliance contracting has emerged as one of the most successful collaborative procurement approaches in recent years, demonstrating remarkable outcomes in complex infrastructure projects. The Melbourne Metro Tunnel Project serves as a prime example, where an alliance model helped deliver $1 billion in cost savings while maintaining superior quality standards.
The success of this approach is further evidenced by the Singapore Sports Hub project, where alliance contracting facilitated seamless integration between design, construction, and operations teams. This resulted in a 30% reduction in delivery time compared to traditional procurement methods and enhanced innovation through shared risk and reward mechanisms.
In Northern Europe, the Stockholm Bypass Project showcases how alliance contracting can effectively manage geological challenges and environmental concerns. The alliance framework enabled rapid problem-solving and decision-making, with stakeholders reporting 40% fewer disputes compared to similar-scale projects using conventional contracts.
Key success factors identified across these cases include:
– Early contractor involvement in design optimization
– Shared risk allocation and transparent cost structures
– Integrated project teams with aligned objectives
– Performance-based incentives driving innovation
– Real-time collaboration and decision-making protocols
The Australian Pacific Highway Upgrade demonstrates how alliance contracting can scale effectively, with multiple work packages delivered simultaneously while maintaining consistent quality standards. This project achieved a 25% improvement in safety performance metrics and delivered 15% under budget through innovative value engineering solutions.
These case studies confirm that alliance contracting excels in complex, high-risk projects where flexibility and collaboration are essential for success.
Sustainable Procurement Innovation
The Netherlands’ Circular Construction Hub
The Netherlands has emerged as a pioneer in circular construction practices, establishing a comprehensive network of material banks and innovative procurement strategies. The Dutch government’s commitment to achieving a fully circular economy by 2050 has catalyzed groundbreaking initiatives across the construction sector.
Amsterdam’s material marketplace serves as a central hub where construction companies can source and trade recycled building materials. This digital platform, launched in 2018, has facilitated the reuse of over 100,000 tons of construction materials, demonstrating the practical viability of circular procurement at scale.
Notable projects include the temporary courthouse in Amsterdam, which incorporated 95% reusable materials, and the Circl pavilion, showcasing how end-of-life planning can be integrated into initial design phases. The Dutch construction industry has developed sophisticated material passports that track building components throughout their lifecycle, enabling future reuse and reducing waste.
The Rotterdam Construction Hub has implemented a pioneering procurement model requiring contractors to demonstrate material circularity plans before bid approval. This approach has reduced virgin material use by 35% across participating projects while maintaining quality standards.
Industry collaboration has been crucial, with organizations like the Dutch Green Building Council developing certification systems specifically for circular construction. These standards have become benchmarks for sustainable material procurement across Europe, influencing policy development and industry practices beyond Dutch borders.
Singapore’s Green Mark Projects
Singapore’s Building and Construction Authority (BCA) has established itself as a global leader in sustainable construction through its Green Mark certification system. The procurement strategies employed in these projects demonstrate a sophisticated approach to achieving environmental objectives while maintaining cost-effectiveness.
Recent data shows that over 40% of Singapore’s buildings have achieved Green Mark certification, with procurement playing a crucial role in this success. The strategy typically involves a three-phase approach: pre-qualification of suppliers based on sustainability credentials, performance-based specifications that emphasize energy efficiency, and lifecycle cost analysis rather than initial cost considerations.
Notable examples include the Keppel Bay Tower, Singapore’s first Green Mark Platinum Zero Energy commercial building. The procurement team implemented an innovative vendor selection process that prioritized suppliers offering advanced green technologies and materials with verified environmental performance data. This approach resulted in a 22.3% reduction in energy consumption compared to standard commercial buildings.
The procurement framework also emphasizes the integration of smart building technologies and sustainable materials. Contractors are required to demonstrate their capability to deliver solutions that meet specific environmental performance indicators, including energy efficiency, water conservation, and waste reduction metrics. This has led to the development of a robust green supply chain ecosystem in Singapore’s construction sector.
These procurement strategies have become a benchmark for sustainable construction projects globally, demonstrating how careful supplier selection and performance-based specifications can drive environmental innovation in the built environment.
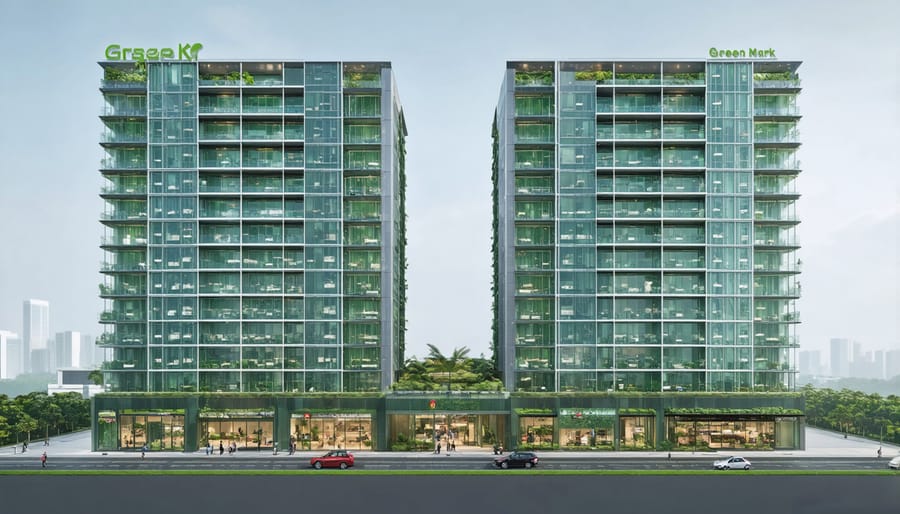
Technology-Driven Procurement Solutions
The construction industry is witnessing a dramatic transformation in procurement processes through the integration of cutting-edge technologies. AI-powered procurement solutions are revolutionizing how materials, equipment, and services are sourced, tracked, and managed throughout the project lifecycle.
Blockchain technology is emerging as a game-changer in construction procurement, enabling transparent and immutable record-keeping of transactions. Major contractors like Skanska and Balfour Beatty have implemented blockchain-based systems that have reduced procurement cycle times by 45% while enhancing supplier verification and contract compliance.
Internet of Things (IoT) sensors are transforming inventory management and supply chain visibility. Smart materials tracking systems using RFID tags and GPS monitoring provide real-time updates on delivery status, storage conditions, and usage patterns. For instance, the Hudson Yards development in New York implemented an IoT-based procurement system that reduced material waste by 30% and improved delivery accuracy to 98%.
Machine learning algorithms are now being deployed to optimize vendor selection and pricing strategies. These systems analyze historical data, market trends, and supplier performance metrics to recommend the most cost-effective procurement decisions. The Dubai Creek Tower project utilized predictive analytics to forecast material requirements six months in advance, resulting in a 15% reduction in procurement costs.
Digital procurement platforms are facilitating seamless collaboration between stakeholders. Cloud-based solutions enable real-time sharing of specifications, automated purchase orders, and integrated payment systems. These platforms have shown to reduce administrative overhead by up to 60% while minimizing errors in procurement documentation.
The integration of these technologies is creating a more efficient, transparent, and cost-effective procurement ecosystem. Construction firms that embrace these innovations are seeing significant improvements in project delivery times, cost control, and risk management. As these technologies continue to evolve, they will play an increasingly crucial role in shaping the future of construction procurement.
The evolution of innovative procurement in construction continues to reshape industry practices, delivering unprecedented efficiencies and value. Through the examples and case studies examined, it’s clear that digital transformation, collaborative delivery models, and sustainable procurement strategies are no longer optional but essential for project success in today’s competitive landscape.
Key learnings demonstrate that successful innovative procurement requires a balanced approach combining technological adoption with human expertise. Organizations that have embraced integrated project delivery, blockchain-based contract management, and AI-powered supplier selection have achieved significant cost reductions while improving project outcomes and stakeholder satisfaction.
Looking ahead, the construction industry can expect further disruption from emerging technologies and procurement methodologies. The rise of digital twins, smart contracts, and automated procurement platforms will continue to streamline processes and enhance decision-making capabilities. Sustainability considerations will increasingly influence procurement strategies, with circular economy principles becoming central to material selection and supplier evaluation.
For construction professionals and organizations to remain competitive, developing adaptive procurement frameworks that can incorporate new technologies and methodologies will be crucial. Investment in digital skills development, sustainable practices, and collaborative partnerships will determine success in future construction projects.
The future outlook suggests a more connected, efficient, and sustainable construction industry, where innovative procurement serves as a cornerstone for project delivery excellence. Organizations that embrace these changes while maintaining focus on practical implementation and measurable outcomes will lead the industry’s transformation.