In today’s high-stakes commercial environment, air conditioner energy efficiency ratings directly impact operational costs, environmental compliance, and long-term facility performance. The Seasonal Energy Efficiency Ratio (SEER) and Energy Efficiency Ratio (EER) serve as critical benchmarks for HVAC system evaluation, with modern units ranging from SEER 13 to SEER 21. Understanding these ratings enables facility managers to optimize their building’s energy consumption while meeting stringent regulatory requirements. Recent industry data indicates that upgrading to higher-efficiency units can reduce energy costs by 20-40%, making efficiency ratings a crucial factor in equipment selection and replacement decisions. This comprehensive analysis explores the technical specifications, cost implications, and strategic considerations that inform air conditioning efficiency investments, providing decision-makers with essential insights for maximizing return on investment while ensuring sustainable building operations.
Understanding AC Energy Efficiency Ratings
SEER vs. EER: Key Differences
SEER (Seasonal Energy Efficiency Ratio) and EER (Energy Efficiency Ratio) represent distinct approaches to measuring air conditioning efficiency, each serving specific evaluation purposes. SEER calculations factor in seasonal temperature variations and partial load operations, providing a comprehensive efficiency metric across an entire cooling season. This rating typically ranges from 13 to 25, with higher numbers indicating superior seasonal performance.
In contrast, EER measures efficiency at a fixed outdoor temperature of 95°F and 50% indoor humidity, offering a snapshot of performance under peak load conditions. EER ratings typically fall between 8 and 14, making them particularly valuable for assessing performance in consistently hot climates or commercial applications where steady-state operation is common.
For commercial facilities, understanding both metrics is crucial. While SEER offers insights into overall seasonal efficiency and operational costs, EER provides critical information about performance during peak demand periods when utility rates are highest. Modern high-efficiency units often achieve SEER ratings above 18 and EER ratings above 12, representing significant improvements over minimum federal standards.
The relationship between these ratings typically follows a pattern where SEER is approximately 1.2 times the EER value. However, this correlation can vary based on equipment design and application specifics. When evaluating new systems, professionals should consider both metrics to ensure optimal performance for their specific climate and usage patterns.
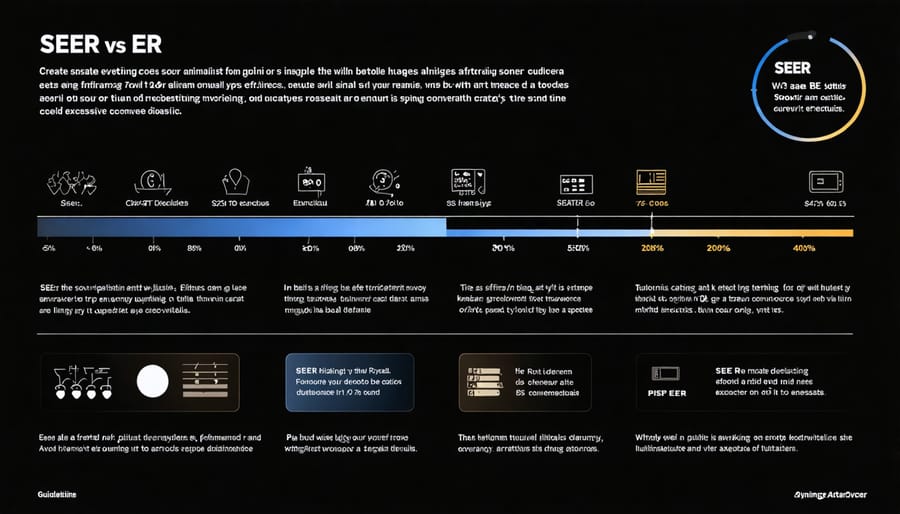
Current Industry Standards and Regulations
The U.S. Department of Energy (DOE) mandates minimum efficiency standards for air conditioning systems through the Seasonal Energy Efficiency Ratio (SEER) rating system. As of January 2023, the minimum SEER requirement for residential split-system air conditioners is 14 SEER in the northern region and 15 SEER in the southern region. For commercial applications, the requirements vary based on system capacity and type.
These standards are further differentiated by geographic regions, with stricter requirements in hot-climate zones. The DOE has established three distinct regions: North, Southeast, and Southwest, each with specific minimum efficiency requirements reflecting local climate conditions and energy demands.
The Energy Independence and Security Act (EISA) requires manufacturers to meet these standards, ensuring all new installations comply with regional minimums. For commercial buildings, ASHRAE Standard 90.1 provides additional guidance, requiring minimum Energy Efficiency Ratio (EER) ratings alongside SEER ratings.
California’s Title 24 sets even more stringent requirements, often exceeding federal standards by 15-20%. The European Union employs a different metric system, the Seasonal Energy Efficiency Ratio (SEER), with ratings typically ranging from A+++ to D.
Compliance with these standards is mandatory for manufacturers and installers, with penalties for non-compliance including fines and product recalls. The DOE regularly updates these requirements, with the next major revision scheduled for 2025, aimed at further improving energy efficiency across the industry.
Cost-Benefit Analysis of High-Efficiency Units
ROI Calculations for Different SEER Ratings
Understanding ROI calculations for different SEER ratings is crucial for implementing effective energy cost reduction strategies in commercial buildings. To calculate potential savings, use the following formula:
Annual Energy Savings = (1/SEER1 – 1/SEER2) × Cooling Load × Operating Hours × Energy Cost
For example, upgrading from a SEER 14 to SEER 18 system in a 50,000 sq ft commercial building:
– Average cooling load: 300,000 BTU/hour
– Annual operating hours: 2,000
– Energy cost: $0.12/kWh
Annual savings = (1/14 – 1/18) × 300,000 × 2,000 × $0.12 = $2,571
The payback period calculation:
ROI Period (years) = Additional Equipment Cost ÷ Annual Energy Savings
Assuming a $5,000 premium for the higher SEER unit:
Payback Period = $5,000 ÷ $2,571 = 1.94 years
Notable ROI patterns across SEER ratings:
– SEER 14 to 16: Average 2-3 year payback
– SEER 16 to 18: Average 3-4 year payback
– SEER 18+: Payback periods typically extend beyond 5 years
Factor in maintenance costs, equipment longevity, and potential utility incentives for more accurate ROI calculations. Higher SEER ratings generally deliver better long-term returns in regions with extended cooling seasons and higher electricity rates.
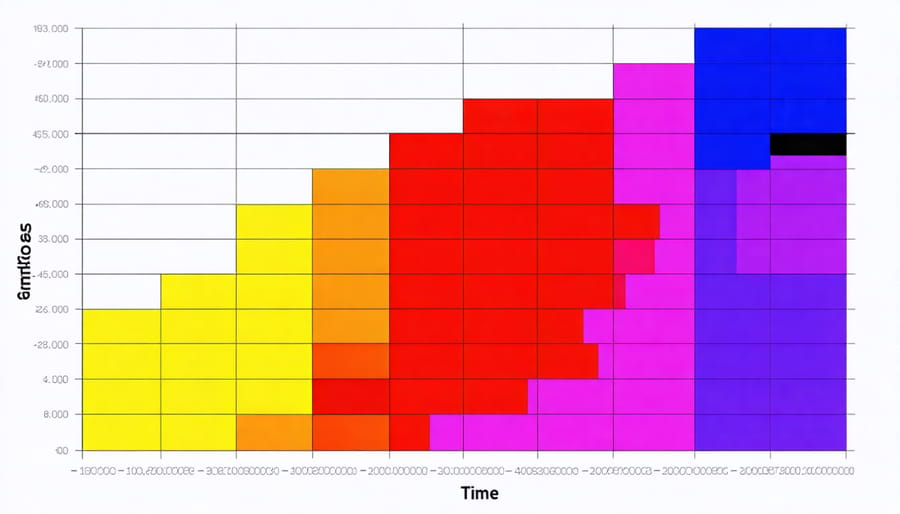
Available Incentives and Rebates
Several federal, state, and utility programs offer substantial financial incentives for implementing energy-efficient HVAC systems. The federal government provides tax credits of up to 10% of the total system cost (maximum $300) for ENERGY STAR certified air conditioners that meet minimum efficiency requirements. Commercial buildings can qualify for additional deductions through the Energy-Efficient Commercial Buildings Tax Deduction (179D).
Many state governments supplement these federal incentives with their own programs. California’s TECH Clean California initiative offers rebates ranging from $3,000 to $10,000 for qualifying commercial HVAC installations. New York’s Clean Heat Program provides similar incentives, with additional bonuses for systems exceeding minimum efficiency standards.
Local utility companies frequently offer custom rebate programs based on energy savings achievements. For example, Pacific Gas & Electric (PG&E) provides rebates of $50-$100 per ton for commercial AC units that exceed Title 24 requirements. Southern California Edison offers performance-based incentives of up to $0.15 per kWh saved annually.
To maximize available incentives, building owners should:
– Consult utility providers about available programs
– Review state energy office websites for current offerings
– Work with qualified contractors familiar with incentive documentation
– Consider timing installations to align with program deadlines
– Maintain detailed records of equipment specifications and costs
Remember that incentive programs are regularly updated, and availability varies by location. Early planning and consultation with energy efficiency experts can help secure optimal financial benefits.
Implementation Strategies for Commercial Buildings
System Sizing and Performance Optimization
Proper system sizing is crucial for maximizing the energy efficiency of air conditioning systems. A correctly sized unit operates at optimal efficiency, avoiding the energy waste associated with oversized systems and the strain of undersized units. Industry best practices recommend conducting a detailed load calculation using ASHRAE standards, accounting for factors such as building envelope characteristics, occupancy patterns, and local climate conditions.
For commercial applications, professionals should implement a two-step sizing approach. First, calculate the base cooling load using modern modeling software that considers thermal mass, solar gain, and internal heat sources. Second, apply a safety factor of 10-15% rather than the traditional 25-30%, as oversizing significantly impacts efficiency ratings and operational costs.
To optimize performance, consider implementing the following strategies:
– Install programmable thermostats with zone control capabilities
– Maintain proper refrigerant charge levels within manufacturer specifications
– Ensure adequate airflow across evaporator and condenser coils
– Schedule regular maintenance including filter replacement and coil cleaning
– Deploy smart building controls for dynamic load management
System placement also affects efficiency. Position outdoor units away from direct sunlight and ensure proper clearance for airflow. For multiple unit installations, maintain minimum spacing requirements to prevent thermal interference. Regular performance monitoring and seasonal adjustments help maintain peak efficiency levels throughout the system’s lifecycle.
Proper commissioning is essential for new installations, including thorough testing and balancing of air distribution systems to ensure designed efficiency ratings are achieved in real-world operation.
Integration with Building Management Systems
Modern energy-efficient air conditioning systems achieve optimal performance through seamless integration with building management systems (BMS). This integration enables real-time monitoring, automated control, and data-driven optimization of HVAC operations across entire facilities.
Advanced BMS platforms utilize IoT sensors and sophisticated algorithms to continuously analyze multiple parameters, including occupancy patterns, thermal loads, and outdoor conditions. This data enables dynamic adjustment of cooling output, reducing energy waste while maintaining optimal comfort levels. Studies indicate that BMS-integrated air conditioning systems can achieve 15-30% greater efficiency compared to standalone units.
Key integration features include:
– Automated scheduling based on occupancy patterns
– Load-based operation optimization
– Predictive maintenance alerts
– Energy consumption tracking and reporting
– Zone-specific temperature control
– Fault detection and diagnostics
For maximum effectiveness, system integration should be considered during the initial design phase. This ensures proper communication protocols are established and necessary sensors are strategically placed. Regular software updates and calibration maintain system efficiency over time.
Building operators can access performance metrics through centralized dashboards, enabling informed decisions about system operations and maintenance schedules. This data-driven approach supports continuous improvement in energy efficiency while extending equipment lifespan.
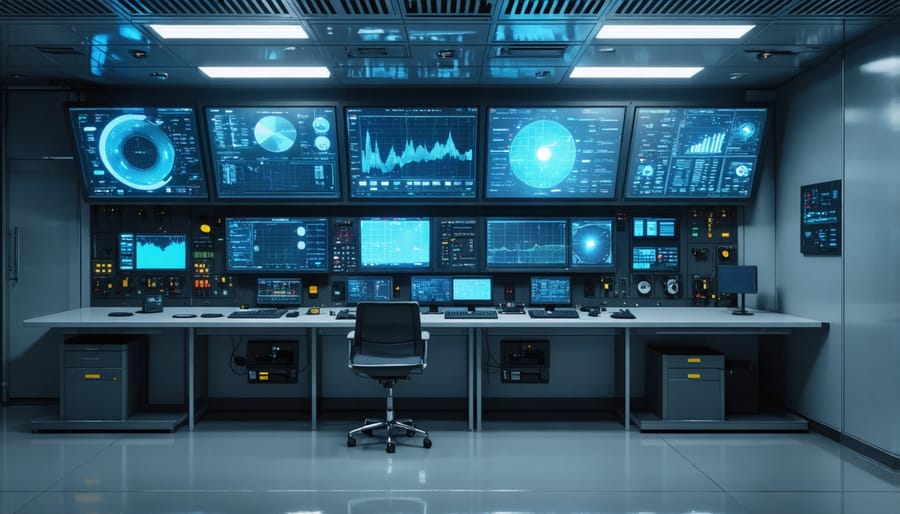
Case Study: High-Efficiency AC Implementation
In 2021, the Summit Corporate Center in Denver, Colorado, underwent a comprehensive HVAC system overhaul that showcases the tangible benefits of implementing high-efficiency air conditioning systems. This building energy efficiency upgrades project involved replacing ten aging 15 SEER units with new 21 SEER variable-speed systems across their 180,000-square-foot facility.
The implementation team, led by chief engineer Marcus Rodriguez, documented a systematic approach to the upgrade. Initial energy audits revealed the existing systems were consuming approximately 45% of the building’s total energy usage. The new installation incorporated advanced features including smart zoning controls, Variable Refrigerant Flow (VRF) technology, and IoT-enabled monitoring systems.
Post-implementation data collected over 18 months showed remarkable improvements:
– 32% reduction in overall cooling energy consumption
– Annual energy cost savings of $87,000
– Peak load reduction of 28%
– ROI achieved within 3.2 years
– Maintenance costs reduced by 40%
The success factors included:
1. Detailed pre-installation analysis of building load patterns
2. Strategic phasing of installation to minimize tenant disruption
3. Integration with existing building management systems
4. Comprehensive staff training on new technology
5. Continuous monitoring and optimization protocols
The project team encountered several challenges, including the need to retrofit existing ductwork and upgrade electrical systems. However, innovative solutions, such as implementing temporary cooling units during installation and conducting work during off-peak hours, helped maintain tenant comfort throughout the transition.
This case study demonstrates that while high-efficiency AC systems require significant upfront investment, the long-term benefits substantially outweigh the initial costs. The Summit Corporate Center’s experience has become a benchmark for similar commercial properties in the region, with several neighboring facilities now implementing comparable upgrades based on these documented results.
Understanding and implementing energy efficiency ratings for air conditioning systems is crucial for optimizing building performance and reducing operational costs. Through careful analysis of SEER, EER, and IEER ratings, construction professionals can make informed decisions that significantly impact both environmental sustainability and financial outcomes.
The key takeaway is that higher efficiency ratings generally translate to lower operating costs and reduced energy consumption, despite higher initial investments. For optimal results, we recommend:
1. Conducting comprehensive energy audits before selecting new AC systems
2. Calculating life-cycle costs rather than focusing solely on purchase price
3. Considering climate-specific factors when evaluating efficiency ratings
4. Implementing regular maintenance schedules to maintain rated efficiency levels
5. Integrating smart building management systems for optimal performance
Industry professionals should prioritize systems with SEER ratings of 16 or higher for maximum energy savings in commercial applications. When evaluating multiple options, factor in utility incentives and rebates that can offset initial costs of high-efficiency units.
Remember that efficiency ratings are just one component of a comprehensive HVAC strategy. Success lies in combining efficient equipment with proper sizing, installation, and ongoing maintenance. By following these recommendations and staying current with evolving efficiency standards, building professionals can ensure their projects deliver optimal performance while meeting increasingly stringent energy requirements.
For best results, partner with certified HVAC professionals and engage energy consultants during the planning phase to maximize system efficiency and ROI.