Automation system integration revolutionizes modern construction by seamlessly connecting disparate building systems into cohesive, intelligent networks that drive operational efficiency and reduce costs by up to 30%. From HVAC controls to security protocols, integrated automation systems serve as the central nervous system of smart buildings, enabling real-time monitoring, predictive maintenance, and data-driven decision-making across all building operations. This transformative technology merges traditional building management systems (BMS) with cutting-edge IoT sensors, artificial intelligence, and cloud computing platforms to create responsive, self-optimizing environments that enhance occupant comfort while minimizing energy consumption.
Construction professionals must understand that successful automation integration requires careful planning across three critical dimensions: system architecture design, protocol compatibility, and scalability requirements. Modern integration projects demand expertise in both legacy systems and emerging technologies, ensuring seamless communication between diverse components while maintaining robust cybersecurity measures. The ROI potential is significant, with properly integrated systems delivering average energy savings of 15-20% and maintenance cost reductions of up to 25% within the first year of implementation.
As building systems become increasingly complex, the role of system integrators has evolved from simple hardware installation to comprehensive solution architecture. Today’s integration specialists must navigate multiple communication protocols, understand cross-platform compatibility issues, and implement sophisticated analytics capabilities that transform raw data into actionable insights for facility managers and building owners.
This comprehensive guide explores the essential components of modern automation system integration, offering practical strategies for successful implementation while addressing common challenges and emerging trends in the construction industry.
The Evolution of Building Energy Management
Traditional vs. Modern Integration Approaches
Traditional building integration approaches relied heavily on standalone systems, with separate controls for HVAC, lighting, and security. These siloed solutions often resulted in operational inefficiencies, higher maintenance costs, and limited scalability. Facility managers had to monitor multiple interfaces, making it challenging to optimize building performance effectively.
Modern integration methods, centered around building automation systems, offer a unified platform that seamlessly connects various building components. This convergence enables real-time monitoring, predictive maintenance, and automated responses to changing conditions. Advanced protocols like BACnet and Modbus facilitate seamless communication between different subsystems, creating a cohesive network that enhances operational efficiency.
The key differences lie in data utilization and system intelligence. While traditional approaches provided basic monitoring capabilities, modern solutions leverage machine learning algorithms to analyze patterns, optimize energy consumption, and predict maintenance needs. Cloud connectivity enables remote management and data analysis, offering unprecedented control over building operations.
Integration costs have also evolved significantly. Although initial investments in modern systems may be higher, the long-term benefits include reduced operational expenses, improved energy efficiency, and enhanced occupant comfort. The ability to integrate future technologies and scale operations makes contemporary approaches more sustainable and future-proof compared to their traditional counterparts.
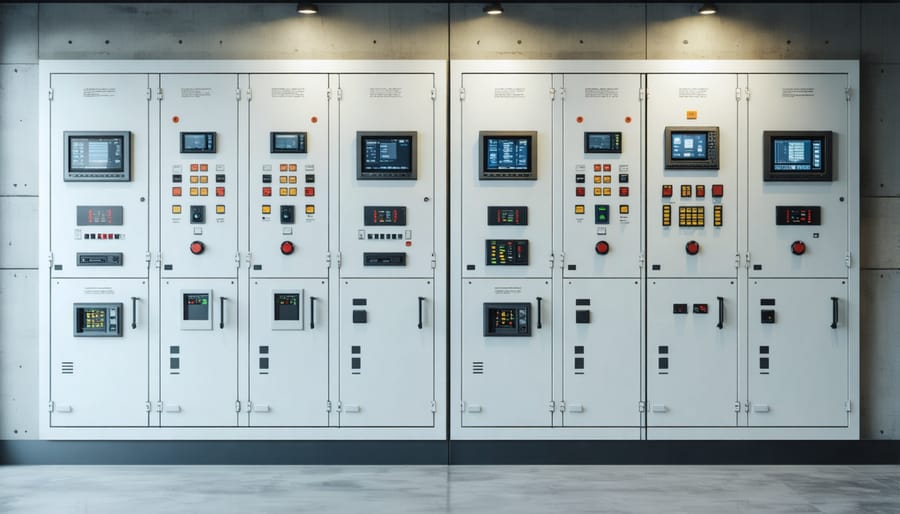
Key Components of Modern Energy Integration
Modern energy integration in automated building systems comprises several interconnected components that work together to optimize energy efficiency and sustainability. At the core lies the Building Management System (BMS), which serves as the central nervous system, coordinating various energy sources and consumption patterns.
Smart meters and advanced monitoring systems provide real-time data collection and analysis, enabling precise control over energy distribution. These systems interface with renewable energy sources, primarily solar panels and wind turbines, through sophisticated power management controllers that regulate energy flow and storage.
Energy storage solutions, including advanced battery systems and thermal storage units, play a crucial role in maintaining consistent power supply. These systems store excess energy during peak production periods and release it during high-demand times or when renewable sources are unavailable.
Load management systems automatically prioritize and distribute power based on predetermined hierarchies and real-time demands. They incorporate predictive algorithms that anticipate energy needs based on historical data, weather forecasts, and occupancy patterns.
Integration protocols and communication standards, such as BACnet and Modbus, ensure seamless interaction between different system components. These protocols facilitate data exchange between renewable energy systems, HVAC controls, lighting systems, and other building automation components.
Fault detection and diagnostic systems continuously monitor performance metrics, identifying potential issues before they impact system efficiency. This predictive maintenance approach helps maintain optimal energy integration performance while reducing operational costs.
Core Integration Technologies
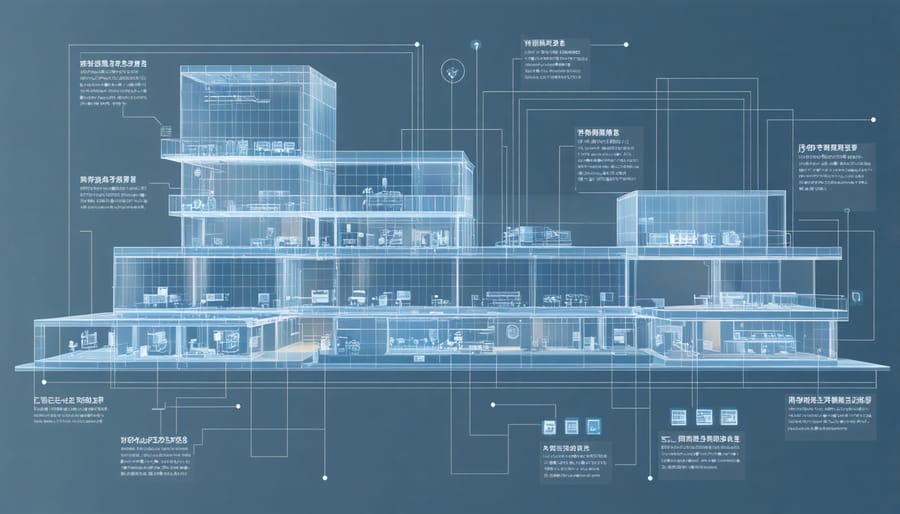
Smart Monitoring and Control Systems
Smart monitoring and control systems represent the backbone of modern automation system integration, enabling real-time oversight and precise management of building operations. These systems utilize advanced sensors, data analytics, and intelligent algorithms to optimize performance across multiple building systems simultaneously.
At the core of these systems are IoT-enabled devices that continuously collect data on various parameters including energy consumption, equipment performance, occupancy patterns, and environmental conditions. This data streams into centralized building management systems (BMS) where it undergoes analysis to identify patterns, predict maintenance needs, and automatically adjust system operations for optimal efficiency.
Advanced monitoring capabilities now include predictive analytics that can forecast potential equipment failures before they occur, allowing maintenance teams to address issues proactively rather than reactively. Machine learning algorithms continuously improve system performance by learning from historical data and adapting to changing conditions.
Control mechanisms have evolved to include sophisticated automation protocols that can manage complex interactions between different building systems. For instance, HVAC systems can automatically adjust based on occupancy data, while lighting controls respond to both natural light levels and space utilization patterns.
The integration of these smart systems provides facility managers with comprehensive dashboards and reporting tools, enabling data-driven decision-making. Remote monitoring capabilities allow for off-site system management, while automated alerts ensure rapid response to any operational anomalies.
Security features are embedded throughout these systems, with encryption protocols and access controls protecting sensitive operational data and preventing unauthorized system access.
Data Analytics and AI Implementation
Modern automation systems leverage advanced data analytics and artificial intelligence to revolutionize building energy management. Recent studies have shown that AI in energy optimization can reduce operational costs by up to 30% while significantly improving system performance.
These intelligent systems continuously collect and analyze data from various building components, including HVAC systems, lighting controls, and occupancy sensors. Machine learning algorithms process this information to identify patterns, predict usage trends, and automatically adjust settings for optimal efficiency. The AI-driven approach enables predictive maintenance, reducing downtime and extending equipment life spans.
Real-time analytics provide facility managers with actionable insights through sophisticated dashboards, allowing for informed decision-making and rapid response to changing conditions. The system can automatically adjust temperature setpoints, lighting levels, and ventilation rates based on occupancy patterns, weather forecasts, and energy pricing data.
Advanced neural networks can learn from historical performance data to create increasingly accurate energy consumption models. These models enable proactive energy management strategies, such as load shifting during peak demand periods and optimizing renewable energy integration. The implementation of such systems typically requires careful planning and coordination between automation specialists, energy managers, and facility operators to ensure seamless integration with existing building management systems.
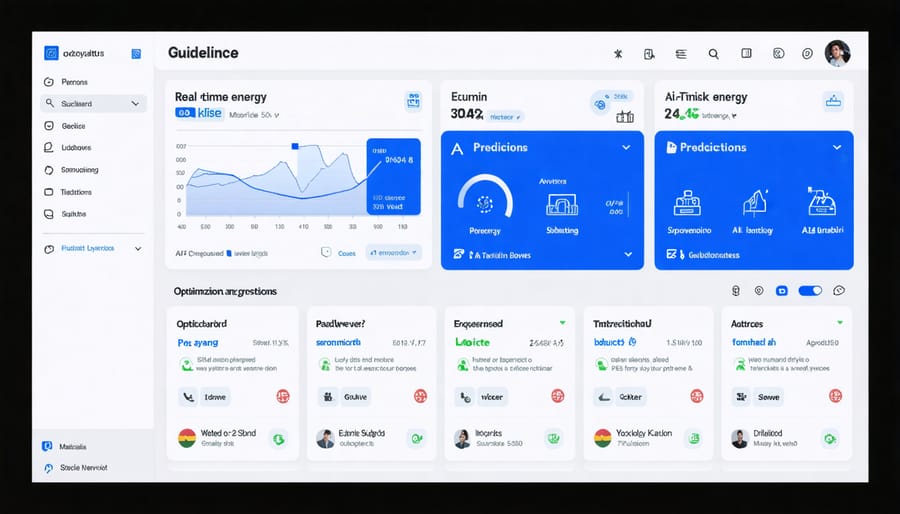
Integration Protocols and Standards
Modern automation system integration relies heavily on standardized integration protocols and communication standards that ensure seamless interoperability between different components and systems. The most widely adopted protocols include BACnet (Building Automation and Control Networks), which has become the de facto standard for building automation systems, and Modbus, particularly valued for its simplicity and reliability in industrial applications.
KNX and LonWorks have established themselves as robust protocols for building control systems, offering comprehensive solutions for lighting, HVAC, and security integration. The emergence of IP-based protocols has further revolutionized system integration, with protocols like BACnet/IP and KNXnet/IP enabling seamless integration with existing IT infrastructure.
For data exchange between different systems, OPC UA (Open Platform Communications Unified Architecture) has gained significant traction, providing a secure and reliable framework for industrial automation integration. Meanwhile, MQTT (Message Queuing Telemetry Transport) has become essential for IoT device integration, offering lightweight communication ideal for remote monitoring and control.
Industry standards such as ISO 16484 for building automation and control systems, and IEC 61499 for distributed automation systems, provide crucial guidelines for system integration, ensuring reliability, security, and long-term maintainability of automated building systems.
Implementation Strategies and Best Practices
Planning and Assessment
Successful automation system integration begins with a comprehensive assessment of the building’s existing infrastructure and future requirements. This evaluation phase typically involves a detailed analysis of current systems, including HVAC, lighting, security, and energy management components. Project managers must identify potential integration points and assess compatibility between different systems and protocols.
The planning process requires creation of a detailed scope document outlining specific integration objectives, technical requirements, and expected outcomes. This document should include performance metrics, system redundancy requirements, and scalability considerations. Teams must also evaluate network infrastructure capabilities and determine if upgrades are necessary to support the integrated automation system.
Risk assessment forms a crucial component of the planning phase. This includes identifying potential points of failure, cybersecurity vulnerabilities, and operational disruptions that could occur during implementation. Stakeholders should develop contingency plans and establish clear protocols for system maintenance and updates.
Cost-benefit analysis must consider both immediate implementation expenses and long-term operational savings. This includes evaluating energy efficiency improvements, reduced maintenance costs, and increased operational effectiveness. The assessment should also factor in training requirements for facility staff and ongoing support needs.
Finally, teams should establish a clear timeline for implementation, including system testing and commissioning phases. This schedule must account for minimal disruption to existing operations while ensuring thorough integration and validation of all automated systems.
System Architecture Design
A well-designed system architecture forms the backbone of successful automation integration in construction projects. The architecture must accommodate both current operational needs and future scalability while ensuring seamless communication between different building systems. This framework typically consists of three primary layers: the field level (sensors and actuators), the automation level (controllers and gateways), and the management level (user interfaces and data analytics).
The field level incorporates various sensors, actuators, and field devices that collect real-time data and execute control commands. These components must be carefully selected based on compatibility, reliability, and environmental conditions. The automation level serves as the system’s nervous system, processing information through programmable logic controllers (PLCs) and building automation controllers (BACs).
At the management level, supervisory control and data acquisition (SCADA) systems provide comprehensive oversight and control capabilities. This layer must feature robust security protocols, intuitive user interfaces, and advanced analytics capabilities for predictive maintenance and optimization.
Modern system architectures increasingly adopt cloud-based solutions and edge computing to enhance processing capabilities and reduce latency. The integration platform should support standard protocols like BACnet, Modbus, and OPC UA to ensure interoperability between different vendors’ systems. Additionally, implementing redundancy and failsafe mechanisms at each architectural layer helps maintain system reliability and continuous operation.
For optimal performance, the architecture should incorporate modular design principles, allowing for easy system expansion and technology updates without disrupting existing operations.
Maintenance and Optimization
Maintaining and optimizing automated systems requires a systematic approach to ensure long-term reliability and peak performance. Regular maintenance schedules should include system diagnostics, component inspections, and performance monitoring to identify potential issues before they impact operations. Implementing predictive maintenance protocols, backed by real-time data analytics, can significantly reduce downtime and extend system longevity.
Successful integration teams develop comprehensive system optimization strategies that encompass both hardware and software components. This includes regular firmware updates, security patches, and performance tuning to maintain system efficiency. Data-driven optimization allows facilities to adjust automation parameters based on usage patterns, environmental conditions, and operational requirements.
Key maintenance practices should focus on:
– Regular calibration of sensors and control systems
– Verification of communication protocols and network integrity
– Assessment of system response times and operational efficiency
– Documentation of maintenance activities and system modifications
– Training updates for maintenance personnel
Optimization efforts should prioritize energy efficiency, operational reliability, and system scalability. By implementing continuous monitoring and improvement processes, organizations can maximize their return on investment while ensuring their automation systems remain current with evolving technological standards and industry requirements.
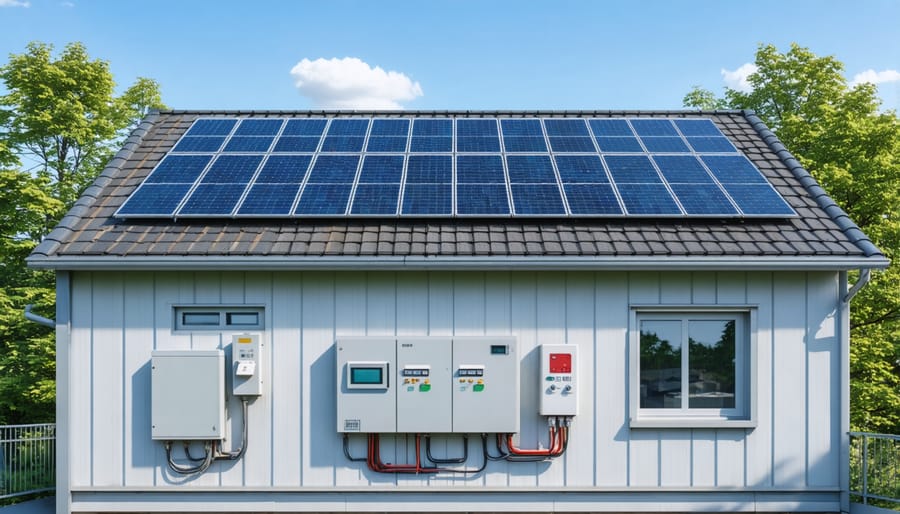
Case Study: Success in Action
The transformation of the Riverside Commercial Plaza in Denver, Colorado, stands as a compelling example of real-world implementation success in automation system integration. This 25-story office building, constructed in 1985, underwent a comprehensive automation upgrade in 2021, resulting in a 40% reduction in energy consumption and significantly improved tenant satisfaction.
The integration project focused on connecting previously isolated building systems, including HVAC, lighting, access control, and energy management. The building’s legacy systems operated independently, leading to inefficiencies and increased operational costs. The integration team, led by SystemTech Solutions, implemented a unified building automation platform that created seamless communication between all subsystems.
Key components of the integration included:
• Installation of smart sensors throughout the building
• Implementation of a centralized building management system
• Integration of occupancy-based lighting and HVAC controls
• Real-time energy monitoring and optimization
• Mobile access for facility managers
The project faced several challenges, particularly in integrating older equipment with modern control systems. The team overcame these obstacles by utilizing middleware solutions and developing custom APIs to ensure compatibility between legacy and new systems.
Results after the first year of operation showed:
• 40% reduction in energy consumption
• 35% decrease in maintenance costs
• 90% improvement in response time to comfort complaints
• 25% increase in tenant satisfaction scores
The success of this project hinged on careful planning and phased implementation. The integration team worked closely with building occupants to minimize disruption during the upgrade process. Regular training sessions were conducted for facility staff to ensure proper system operation and maintenance.
The Riverside Plaza project demonstrates how thoughtful automation system integration can transform an aging commercial building into a modern, efficient facility. The building now serves as a model for similar integration projects across the region, proving that substantial returns on investment are achievable through strategic automation upgrades.
The integration of automated renewable energy systems in buildings represents a pivotal advancement in construction technology, offering substantial benefits that extend beyond mere energy efficiency. Organizations implementing these systems consistently report 20-30% reductions in energy consumption, improved operational efficiency, and enhanced building performance through real-time monitoring and adjustment capabilities.
Looking ahead, the future of automated renewable energy integration appears increasingly promising. Industry experts predict that artificial intelligence and machine learning will further optimize these systems, enabling predictive maintenance and even more sophisticated energy management. The convergence of IoT sensors, smart grid technologies, and renewable energy automation is expected to create buildings that not only consume energy more efficiently but also actively participate in grid stabilization and energy trading.
Several emerging trends indicate continued growth in this sector, including the development of more sophisticated battery storage systems, enhanced integration with microgrids, and improved interoperability between different automation platforms. The increasing focus on carbon neutrality and stringent environmental regulations will likely accelerate the adoption of these technologies across the construction industry.
For construction professionals and building owners, the message is clear: automated renewable energy integration is no longer just an option but a necessity for future-proof buildings. The return on investment continues to improve as technology costs decrease and energy prices rise, making these systems increasingly attractive from both environmental and financial perspectives.