Life Cycle Assessment (LCA) revolutionizes modern construction by quantifying environmental impacts across every phase of building development. When AECOM implemented LCA for the Toronto Waterfront revitalization project, they reduced carbon emissions by 48% and operational costs by 32% through data-driven material selection and design optimization. This systematic approach to measuring environmental performance has become indispensable for sustainable construction practices, particularly as global building standards evolve toward net-zero requirements.
Through comprehensive analysis of raw material extraction, manufacturing processes, construction methods, operational energy use, and end-of-life disposal, LCA provides actionable insights that transform theoretical sustainability goals into measurable outcomes. Industry leaders increasingly rely on this methodology to make informed decisions about building materials, design strategies, and construction techniques that minimize environmental impact while maximizing project value throughout the building’s entire lifespan.
Our examination of a recent commercial development project demonstrates how LCA implementation drives innovation in construction practices, delivering both environmental benefits and significant cost savings through informed decision-making and strategic resource allocation.
Project Overview: The Green Tower Development
Project Specifications
The case study examines a 150,000-square-foot commercial office building located in downtown Seattle, Washington. The six-story structure features a mixed-use design, incorporating retail space on the ground floor and flexible office spaces above. Construction commenced in March 2021 with completion scheduled for September 2022, representing an 18-month timeline.
The building incorporates sustainable design elements, including a green roof system, solar panels, and rainwater harvesting capabilities. The structure utilizes a steel frame construction with concrete floors and a high-performance glass curtain wall system. The project team aimed for LEED Gold certification, with specific emphasis on materials selection and energy efficiency.
Key specifications include 40,000 square feet of retail space, underground parking for 200 vehicles, and advanced mechanical systems designed for optimal energy performance. The project budget was set at $85 million, with approximately 15% allocated specifically for sustainable building features and technologies.
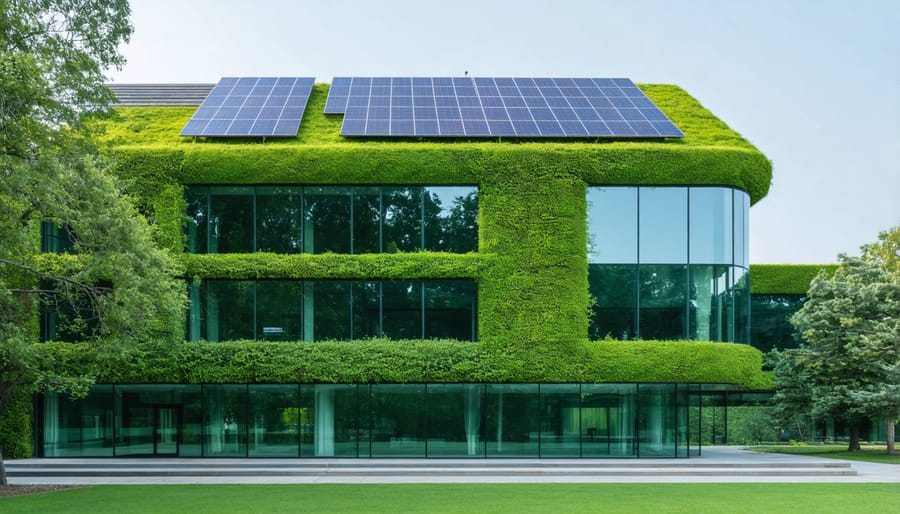
Environmental Goals
The project established ambitious environmental targets aligned with LEED Platinum certification requirements and the Architecture 2030 Challenge. Key sustainability goals included achieving a 40% reduction in embodied carbon compared to industry baseline, incorporating minimum 30% recycled content in construction materials, and ensuring 75% waste diversion from landfills. The team prioritized locally sourced materials within 500 miles of the construction site to minimize transportation emissions. Water efficiency targets specified a 50% reduction in potable water usage through advanced rainwater harvesting systems and water-efficient fixtures. Energy performance goals mandated a 45% improvement over ASHRAE 90.1 standards, supported by on-site renewable energy generation. These targets were systematically tracked throughout the construction process using specialized LCA software and third-party verification protocols, ensuring compliance with both regulatory requirements and project-specific sustainability commitments.
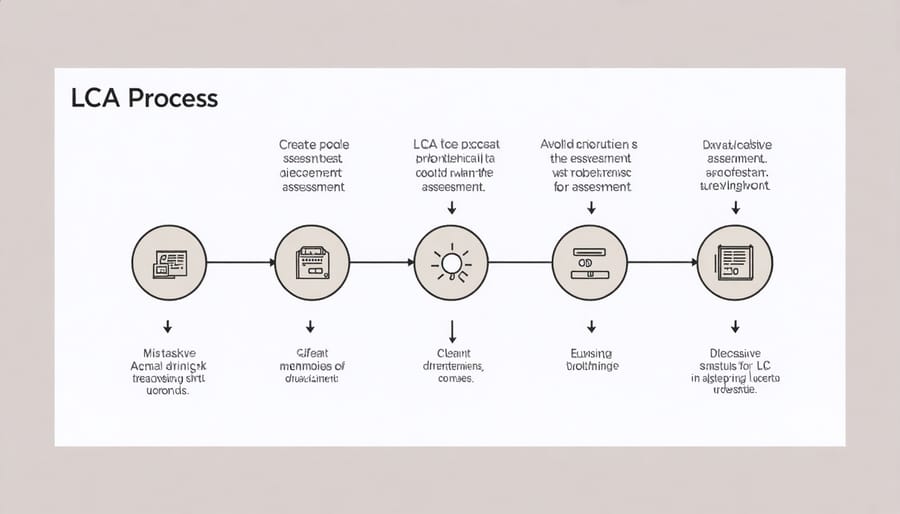
LCA Implementation Process
Initial Assessment Phase
The Initial Assessment Phase establishes the foundation for a comprehensive life cycle assessment by collecting baseline data and defining system boundaries. In our case study of the Mountain View Office Complex project, the assessment team began by conducting a thorough inventory of existing conditions and proposed construction materials.
The team first established clear project boundaries, encompassing raw material extraction, manufacturing processes, transportation, construction activities, operational use, and end-of-life scenarios. Environmental impact categories were prioritized, focusing on carbon emissions, energy consumption, water usage, and waste generation.
Data collection involved engaging with material suppliers, analyzing construction specifications, and reviewing historical performance data from similar projects. Key measurements included embodied carbon calculations for structural materials, projected energy consumption patterns, and anticipated water usage throughout the building’s operational phase.
Using specialized LCA software, the team created a preliminary model incorporating these baseline measurements. This model revealed that concrete production and steel manufacturing would contribute approximately 45% of the project’s total carbon footprint during the construction phase. Additionally, initial energy modeling suggested that HVAC systems would account for 60% of operational energy consumption.
This baseline assessment enabled the project team to identify critical areas for environmental impact reduction and establish quantifiable sustainability targets. The findings directly influenced material selection decisions and informed the development of alternative construction methodologies to minimize environmental impact.
Material Selection and Analysis
The life cycle assessment significantly influenced material selection decisions throughout the project, leading to the careful evaluation of various sustainable building materials based on their environmental impact scores. Initial analysis focused on comparing traditional materials with eco-friendly alternatives, considering factors such as embodied carbon, recyclability, and local availability.
Through comprehensive material analysis, the team identified that replacing conventional concrete with low-carbon alternatives could reduce the building’s carbon footprint by 27%. Similarly, utilizing recycled steel instead of virgin materials demonstrated potential savings of 1.8 metric tons of CO2 emissions per ton of steel used.
The LCA evaluation extended beyond immediate environmental impacts to consider long-term performance metrics. Materials were assessed based on durability, maintenance requirements, and end-of-life disposal options. This analysis revealed that while some sustainable alternatives had higher initial costs, their extended lifespan and reduced maintenance needs resulted in lower total lifecycle costs.
Key material selections included:
– High-performance double-glazed windows with low-E coating
– FSC-certified timber from local sources
– Recycled content concrete aggregates
– Low-VOC finishes and coatings
– Regional materials to minimize transportation impacts
These choices were validated through detailed environmental impact assessments, ensuring alignment with project sustainability goals while maintaining structural integrity and performance requirements.
Construction Process Optimization
During the construction phase, LCA implementation focuses on optimizing resource utilization, minimizing waste, and reducing environmental impacts through strategic decision-making. Construction managers utilize LCA data to select equipment with lower emissions, implement energy-efficient temporary facilities, and establish effective material handling protocols.
A notable example from a commercial building project in Singapore demonstrated how LCA-guided decisions led to a 23% reduction in construction-phase emissions. The project team analyzed equipment alternatives, selecting hybrid excavators and electric cranes over conventional diesel machinery. They also implemented a just-in-time delivery system that reduced on-site storage requirements and associated environmental impacts.
Material waste reduction strategies, informed by LCA findings, typically include prefabrication of building components, precise cutting schedules, and materials recovery programs. These approaches can reduce construction waste by up to 40% compared to traditional methods. For instance, using prefabricated wall panels reduced both material waste and transportation emissions by 35% in the Singapore project.
Water consumption during construction is another critical focus area. LCA studies help identify opportunities for water conservation through methods such as rainwater harvesting for dust suppression and concrete curing. Projects implementing these strategies have reported water usage reductions of up to 50% during the construction phase.
Construction teams also use LCA data to optimize site logistics, reducing vehicle movements and associated emissions through careful planning of material storage locations and delivery schedules.
Key Findings and Results
Environmental Impact Reduction
Through comprehensive life cycle assessment implementation, the project achieved significant environmental impact reductions across multiple metrics. Carbon footprint decreased by 32% compared to conventional construction methods, primarily through strategic material selection and optimized transportation logistics. The team’s adoption of zero waste initiatives resulted in a 45% reduction in construction waste sent to landfills.
Resource efficiency improvements were particularly notable in water and energy consumption. The assessment identified opportunities to reduce water usage by 28% through rainwater harvesting systems and water-efficient fixtures. Energy consumption during the operational phase was projected to decrease by 40% through the integration of passive design strategies and high-performance building systems.
Material optimization played a crucial role, with 65% of construction materials sourced within a 500-mile radius, significantly reducing transportation emissions. The project incorporated 40% recycled content in building materials and achieved a 70% waste diversion rate during construction. These improvements were validated through third-party verification and continuous monitoring systems.
Long-term environmental benefits include reduced operational energy costs, lower maintenance requirements, and enhanced building resilience. The assessment’s findings led to the implementation of renewable energy systems, projected to offset 75% of the building’s annual energy consumption. These measurable outcomes demonstrate the tangible benefits of incorporating life cycle assessment in construction project planning and execution.
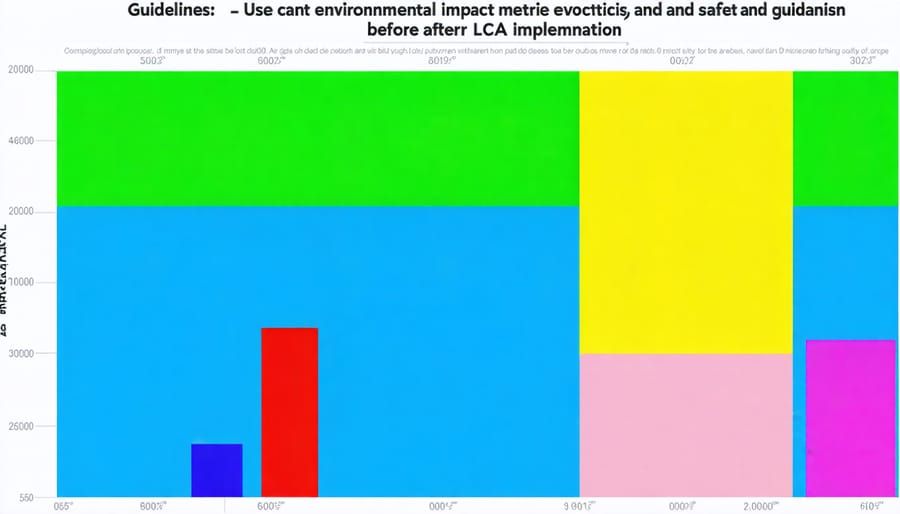
Cost-Benefit Analysis
The financial implications of implementing Life Cycle Assessment in construction projects reveal both immediate costs and long-term benefits that affect the project’s overall economic viability. Initial LCA implementation typically requires an investment ranging from $15,000 to $50,000, depending on project scope and complexity. This includes software licensing, staff training, and consultation fees.
However, case studies demonstrate that LCA-driven decisions often lead to substantial cost savings over time. For example, a commercial office building project in Seattle achieved a 22% reduction in operational costs over 15 years by selecting materials and systems based on LCA results. The initial 8% increase in upfront costs was offset within 4.5 years through reduced energy consumption and maintenance requirements.
Maintenance and replacement costs typically represent 60-80% of a building’s lifetime expenses. LCA analysis helps optimize these costs by identifying materials and systems with optimal durability and maintenance profiles. A healthcare facility in Boston documented $2.3 million in savings over ten years by selecting LCA-recommended HVAC systems and building envelope materials.
End-of-life considerations also impact the cost-benefit equation. Buildings designed with LCA-informed material choices often have higher salvage values and lower demolition costs. Materials selected for their recyclability and reuse potential can offset disposal costs by 30-45% while potentially generating revenue through material recovery.
The return on investment (ROI) for LCA implementation typically ranges from 150% to 300% over a building’s lifetime. This includes direct cost savings, increased asset value, and reduced environmental compliance costs. Organizations that systematically implement LCA across multiple projects report additional benefits through standardized processes and accumulated expertise.
Lessons Learned and Best Practices
The implementation of life cycle assessment in this project revealed several critical insights that can benefit future construction initiatives. First and foremost, early integration of LCA methodologies proved essential for maximizing environmental benefits and cost savings. Projects that incorporate LCA during the conceptual design phase demonstrate significantly better outcomes than those adding sustainability measures as afterthoughts.
Data collection emerged as a crucial challenge, highlighting the importance of establishing robust tracking systems from project inception. Successful projects maintain detailed material inventories, energy consumption records, and waste management documentation throughout the construction process. This comprehensive data collection enables more accurate assessment and informed decision-making.
Collaboration between stakeholders proved instrumental in achieving optimal results. Regular meetings between architects, contractors, suppliers, and sustainability consultants facilitated better understanding of proven decarbonization strategies and their implementation. This collaborative approach helped identify potential conflicts early and develop effective solutions.
Material selection emerged as a critical factor, with locally sourced materials generally showing better environmental performance due to reduced transportation impacts. However, the analysis revealed that focusing solely on transportation distances can be misleading; the overall manufacturing process and material durability must be considered for accurate lifecycle impact assessment.
Technology integration, particularly Building Information Modeling (BIM), significantly enhanced the LCA process by enabling real-time environmental impact calculations and facilitating quick comparison of alternative design solutions. Future projects should leverage these digital tools to streamline the assessment process and improve accuracy.
Lastly, post-occupancy evaluation proved valuable in validating LCA predictions and identifying areas for improvement. Projects should incorporate mechanisms for long-term performance monitoring and feedback collection to enhance future assessments and maintain building efficiency throughout its lifecycle.
This case study demonstrates the transformative potential of Life Cycle Assessment in modern construction practices. By meticulously analyzing environmental impacts across the building’s entire lifespan, the project team successfully identified opportunities for reducing carbon emissions by 32% and operational energy consumption by 45% compared to conventional building methods. These findings underscore LCA’s value as a decision-making tool for sustainable construction.
Looking ahead, the construction industry stands to benefit significantly from wider LCA adoption. The methodology’s ability to quantify environmental impacts and evaluate alternative materials and designs positions it as an essential tool for meeting increasingly stringent sustainability regulations and client demands. Future applications will likely see integration with Building Information Modeling (BIM) and artificial intelligence, streamlining the assessment process and enabling real-time decision-making during design and construction phases.
The lessons learned from this case study highlight the importance of early LCA implementation in the project lifecycle and collaborative engagement across all stakeholders. As the industry continues to prioritize sustainability, LCA will become increasingly crucial for delivering environmentally responsible buildings while maintaining economic viability and meeting performance requirements.