Effective material management on construction sites directly impacts project timelines, costs, and sustainability outcomes. Modern construction demands precision tracking of resources, from structural steel to finishing materials, with research showing that poor material management can increase project costs by up to 15-20%. Digital inventory systems, integrated with IoT sensors and real-time tracking capabilities, now enable project managers to maintain optimal stock levels while preventing costly delays and waste. By implementing structured material management protocols, construction firms can significantly reduce storage costs, minimize material damage, and enhance overall project efficiency.
Today’s construction landscape requires a sophisticated approach to material handling, combining traditional best practices with emerging technologies. Advanced material management systems help construction teams maintain precise control over supply chains, storage conditions, and usage patterns. These systems prove particularly crucial in urban construction sites where space constraints and just-in-time delivery requirements present unique challenges. Through strategic material management, construction firms can achieve substantial improvements in operational efficiency while meeting increasingly stringent environmental standards and project deadlines.
The integration of robust material management practices represents a fundamental shift from reactive to proactive construction site operations. This systematic approach ensures materials arrive when needed, are stored properly, and are utilized efficiently throughout the project lifecycle. By mastering material management, construction firms position themselves for enhanced profitability, improved project outcomes, and sustainable growth in an increasingly competitive industry.
Digital Material Tracking Systems: The New Industry Standard
Real-Time Inventory Management
Real-time inventory management has revolutionized construction site material handling through the integration of advanced tracking technologies. Modern construction sites are increasingly adopting IoT sensors, RFID tags, and cloud-based inventory systems to maintain precise control over material quantities, locations, and consumption rates.
These digital solutions enable project managers to monitor stock levels continuously, receiving instant alerts when materials fall below predetermined thresholds. For example, concrete sensors can track usage patterns and automatically trigger reorder notifications, preventing costly project delays due to material shortages.
Mobile applications connected to central databases allow field workers to scan and update inventory records instantly using smartphones or tablets. This real-time visibility helps prevent common issues such as overordering, material waste, and theft, while ensuring optimal resource allocation across different work zones.
The implementation of BIM (Building Information Modeling) integration with inventory systems provides additional benefits, allowing teams to compare actual material usage against planned requirements. This data-driven approach enables more accurate forecasting and helps identify potential bottlenecks before they impact project timelines.
Case studies have shown that construction companies implementing real-time inventory management systems typically achieve a 15-20% reduction in material waste and a 30% improvement in procurement efficiency. These systems also contribute to better cash flow management by optimizing order quantities and timing based on actual project progress and requirements.
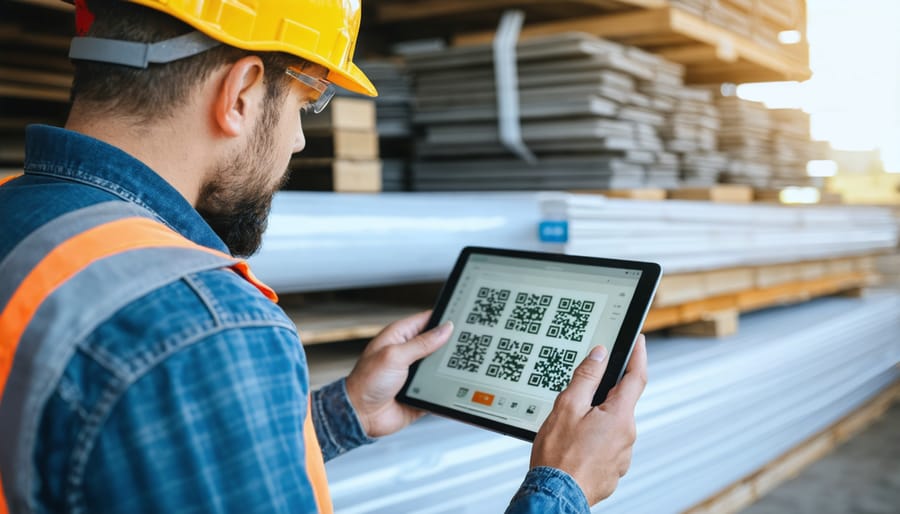
Automated Ordering and Reordering Systems
Automated ordering and reordering systems represent a significant advancement in construction site material management, utilizing sophisticated software algorithms to streamline procurement processes. These systems monitor inventory levels in real-time and automatically generate purchase orders when materials reach predetermined thresholds, eliminating manual tracking and reducing human error.
Modern construction management platforms integrate threshold-based ordering functionality, which allows project managers to set minimum stock levels for critical materials. When inventory drops below these thresholds, the system triggers automatic reorder notifications or directly places orders with pre-approved suppliers, ensuring continuous material availability while optimizing storage space and cash flow.
According to industry studies, construction sites implementing automated ordering systems report a 30% reduction in stockouts and a 25% decrease in excess inventory costs. These systems typically feature customizable parameters for different material categories, accounting for factors such as lead times, seasonal variations, and project phase requirements.
Advanced solutions also incorporate predictive analytics to anticipate material needs based on project schedules and historical usage patterns. This proactive approach helps prevent delays and maintains optimal inventory levels throughout the project lifecycle. Integration with supplier databases enables real-time price comparison and automatic selection of the most cost-effective options while maintaining quality standards.
For maximum efficiency, these systems often include features for automated invoice reconciliation, delivery tracking, and performance analytics, providing comprehensive control over the material procurement cycle.
Storage and Handling Best Practices
Site Layout Planning
Effective site layout planning is crucial for optimizing material flow and minimizing handling costs on construction sites. The placement of materials should follow a strategic approach that considers both immediate needs and long-term project requirements. Storage areas must be designated based on material type, usage frequency, and protection requirements while maintaining clear access routes for equipment and personnel.
Key considerations include establishing dedicated unloading zones near site entrances, creating buffer zones between storage and work areas, and positioning frequently used materials closer to their installation points. Material storage should be organized in a way that follows the construction sequence, with items needed first being more readily accessible.
The layout should incorporate proper spacing between different material categories to prevent cross-contamination and damage. Critical factors include maintaining adequate clearance for vehicle movement, ensuring materials are stored on level ground, and implementing proper drainage systems to prevent water accumulation.
For larger sites, implementing a zone-based system helps streamline material distribution. This approach involves dividing the site into distinct areas, each with its own storage and staging locations. Digital site mapping tools can assist in optimizing these layouts, allowing for real-time adjustments as project needs evolve.
Safety considerations must be integrated into the layout design, including fire breaks between combustible materials, clear emergency access routes, and appropriate spacing for crane operations. Regular review and adjustment of the layout plan ensure continued efficiency as the project progresses.
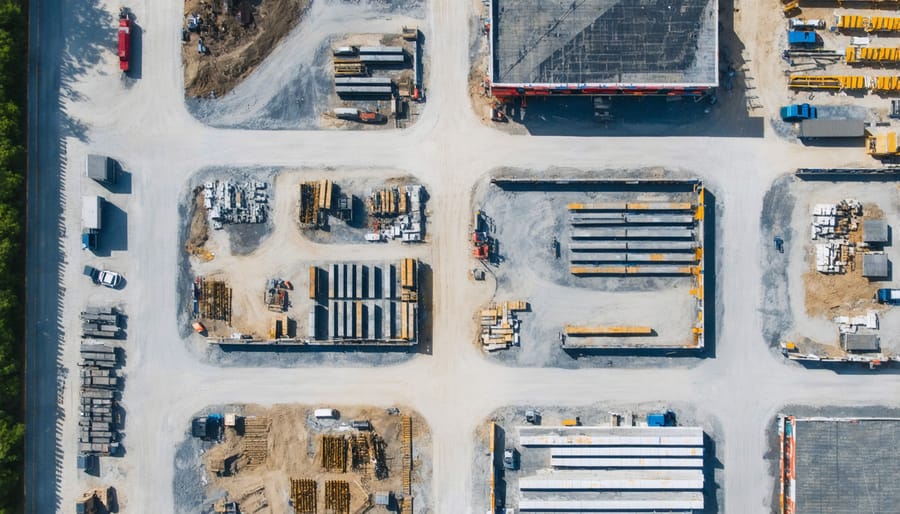
Weather Protection Strategies
Effective weather protection strategies are crucial for maintaining material integrity and preventing costly damages on construction sites. The implementation of proper protective measures begins with a comprehensive weather risk assessment specific to the project location and seasonal conditions.
For moisture-sensitive materials like wood, drywall, and insulation, elevated storage platforms and heavy-duty waterproof covers are essential. These materials should be stored on well-drained surfaces with proper air circulation to prevent moisture accumulation. Specialized storage containers with climate control capabilities offer optimal protection for high-value or particularly vulnerable materials.
Temperature fluctuations can significantly impact construction materials. Concrete curing requires careful temperature monitoring and protection using insulated blankets during cold weather, while steel components need protection from extreme heat to prevent thermal expansion issues. UV-resistant covers help protect plastics and other sun-sensitive materials from degradation.
Site drainage systems play a crucial role in weather protection. Implementing proper grading, temporary drainage channels, and water pumps helps prevent water accumulation around material storage areas. For wind protection, securing materials with appropriate tie-downs and creating windbreaks using temporary fencing or strategic placement of storage containers is essential.
Regular inspection and maintenance of weather protection systems, coupled with real-time weather monitoring, ensure the effectiveness of these protective measures. Having an emergency response plan for extreme weather events completes a comprehensive weather protection strategy.
Safety Protocols in Material Handling
Safety protocols in material handling form the cornerstone of efficient construction site management and worker protection. Proper implementation of these protocols begins with comprehensive risk assessment and clear communication of safety procedures to all personnel involved in material handling operations.
Material storage areas must be clearly demarcated with appropriate signage and barriers. Heavy materials should be stored at ground level whenever possible, with proper support structures to prevent shifting or collapse. For multi-level storage, weight limits must be strictly observed, and materials must be properly secured to prevent falling hazards.
Personal protective equipment (PPE) requirements should be strictly enforced, including hard hats, safety shoes, gloves, and high-visibility clothing. When handling hazardous materials, specialized PPE such as respirators or chemical-resistant gear may be necessary.
Mechanical handling equipment, including cranes, forklifts, and hoists, must be regularly inspected and maintained according to manufacturer specifications. Only certified operators should be permitted to operate such equipment, and clear communication protocols must be established for coordinating lifts and material movement.
Loading and unloading zones should be designated away from high-traffic areas, with adequate space for vehicle maneuvering. Weather conditions must be considered when planning material handling operations, particularly for wind-sensitive materials or during adverse weather.
Emergency response procedures should be clearly documented and regularly practiced, including protocols for material spills, accidents, and equipment failures. Regular safety training and updates ensure all workers remain current with best practices and site-specific requirements.
Supply Chain Integration
Supplier Relationship Management
Effective supplier relationship management is crucial for maintaining a smooth flow of materials to construction sites. Building and nurturing strong partnerships with suppliers goes beyond simple transaction-based relationships, requiring a strategic approach that benefits both parties.
Key to successful supplier relationships is establishing clear communication channels and expectations from the outset. This includes developing detailed service level agreements (SLAs) that outline delivery schedules, quality standards, and response times for urgent requirements. Regular performance reviews help maintain accountability and provide opportunities for continuous improvement.
Implementation of collaborative technology platforms enables real-time information sharing between contractors and suppliers. These systems can automate purchase orders, track deliveries, and provide instant updates on stock levels, helping prevent costly delays and miscommunications.
Strategic partnerships with key suppliers often lead to preferential pricing, priority delivery schedules, and better payment terms. However, it’s essential to maintain relationships with multiple suppliers to mitigate supply chain risks and ensure competitive pricing. Regular market analysis helps identify new suppliers and keeps existing ones competitive.
Developing a supplier rating system based on key performance indicators (KPIs) such as delivery reliability, quality consistency, and pricing competitiveness helps in making informed decisions about supplier partnerships. This data-driven approach enables construction companies to identify top-performing suppliers and address issues with underperforming ones.
Regular supplier meetings and workshops facilitate knowledge sharing and innovation. These sessions can lead to process improvements, cost reductions, and the introduction of new materials or technologies that benefit both parties. They also help suppliers better understand project requirements and challenges, leading to more proactive problem-solving approaches.
Just-in-Time Delivery Coordination
Just-in-time delivery systems have revolutionized construction site material management by minimizing on-site storage requirements and reducing waste. This approach requires precise coordination between suppliers, contractors, and site managers to ensure materials arrive exactly when needed for specific construction phases.
Successful implementation depends on detailed scheduling and real-time communication. Project managers must develop accurate delivery schedules that align with construction timelines, considering factors such as weather conditions, site access restrictions, and labor availability. Digital planning tools and construction management software are essential for maintaining this delicate balance.
To optimize JIT delivery coordination, construction sites should establish designated delivery zones and implement strict time slots for material arrivals. This prevents congestion and ensures efficient unloading processes. Project managers should also maintain buffer times between deliveries to accommodate unexpected delays or schedule changes.
Quality control becomes particularly crucial in JIT systems, as there’s limited time for material inspection between delivery and installation. Implementing pre-delivery quality agreements with suppliers and establishing clear acceptance criteria helps maintain project standards while keeping operations flowing smoothly.
Risk mitigation strategies are essential for JIT success. These include maintaining relationships with multiple suppliers, establishing clear communication protocols, and developing contingency plans for potential delivery disruptions. Some construction sites implement hybrid systems, keeping critical materials in minimal stock while applying JIT principles to bulk items.
Modern technology, including RFID tracking and real-time delivery monitoring systems, enables better coordination and provides valuable data for continuous improvement of delivery processes. This data-driven approach helps refine scheduling accuracy and optimize resource allocation over time.
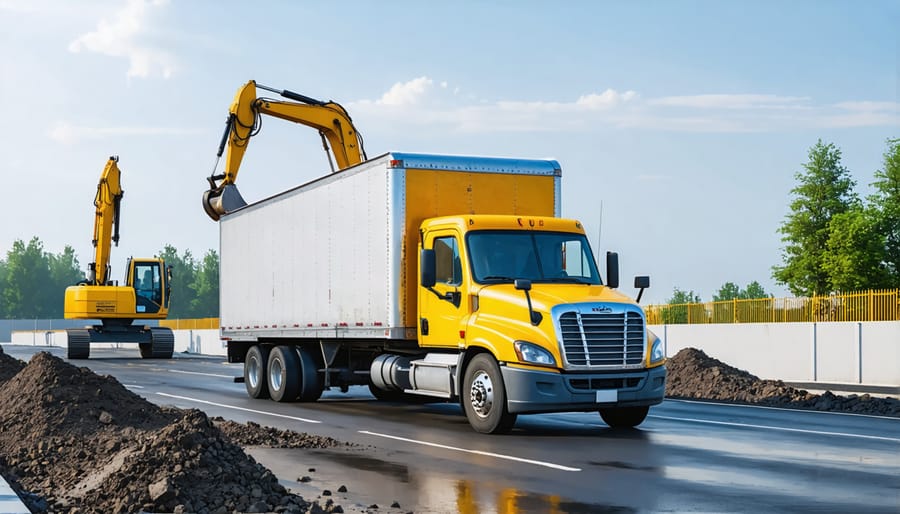
Waste Reduction and Sustainability
Material Usage Optimization
Implementing effective material efficiency techniques is crucial for maintaining project profitability and reducing waste. Start by conducting detailed quantity takeoffs and implementing a just-in-time delivery system to minimize excess inventory. Utilize Building Information Modeling (BIM) software to accurately calculate material requirements and identify potential clashes before construction begins.
Establish standardized cutting procedures for materials like lumber, steel, and drywall to maximize usage from standard sizes. Create detailed cutting lists and implement a systematic approach to material allocation, ensuring larger pieces are used for primary applications while smaller offcuts are repurposed for secondary needs.
Consider prefabrication opportunities where possible, as this typically results in 20-30% less material waste compared to on-site fabrication. Implement a waste tracking system to identify areas of excessive material loss and establish benchmarks for improvement. Regular monitoring of material consumption patterns helps identify opportunities for optimization.
Train site personnel in proper material handling and cutting techniques, emphasizing the importance of precision and planning. Establish a material return policy for unused items and create designated areas for storing reusable materials. Regular audits of material usage patterns can help identify trends and opportunities for further optimization, ultimately contributing to both cost savings and environmental sustainability.
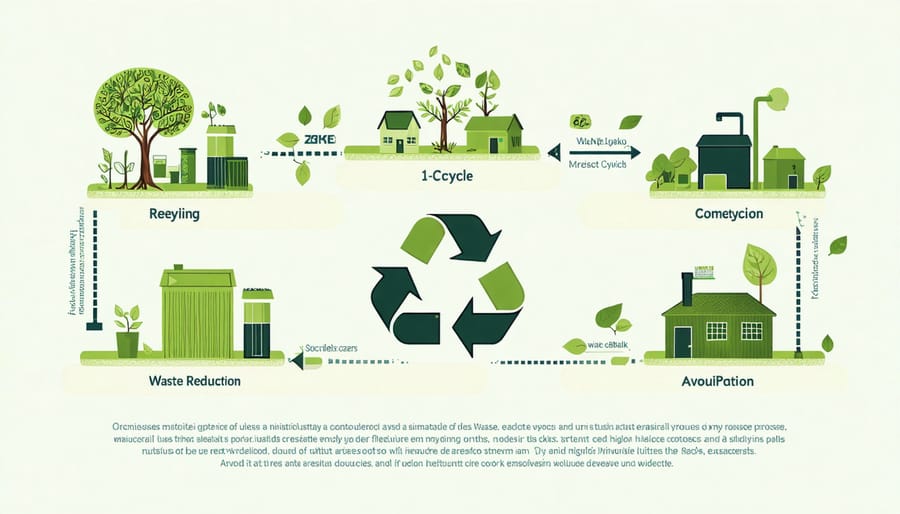
Recycling and Reuse Programs
Implementing effective recycling and reuse programs on construction sites is crucial for sustainable material management and cost reduction. Industry leaders have found that well-structured programs can divert up to 90% of construction waste from landfills while generating significant cost savings.
A comprehensive recycling program should begin with a detailed waste audit to identify recyclable materials commonly generated on-site. Key materials typically include concrete, wood, metal, drywall, and packaging materials. Establishing dedicated sorting areas with clearly marked containers for different material types ensures efficient separation at the source.
Many successful construction firms partner with specialized recycling facilities that can process mixed construction waste. These facilities use advanced sorting technologies to maximize material recovery and often provide detailed reporting for sustainability documentation and LEED certification requirements.
Material reuse strategies focus on identifying salvageable items during demolition phases and storing them properly for future use. Common reusable materials include doors, windows, fixtures, and structural elements. Creating an inventory management system for these items helps track availability and facilitates their incorporation into new projects.
On-site crushing and processing of concrete and masonry waste for use as aggregate or fill material has become increasingly common, reducing transportation costs and environmental impact. Some innovative projects have achieved closed-loop systems where processed materials are immediately incorporated into new construction phases.
To ensure program success, regular training sessions for workers and clear communication of recycling protocols are essential. Monitoring and reporting systems help track diversion rates and identify areas for improvement.
Effective construction site material management is fundamental to project success, combining strategic planning, technological integration, and sustainable practices. Throughout this comprehensive guide, we’ve explored the essential elements that contribute to efficient material handling and resource optimization on construction sites.
The implementation of digital tracking systems has emerged as a crucial factor in modern construction management, enabling real-time inventory monitoring and reducing material waste. By adopting these technologies, construction firms can significantly improve their operational efficiency while maintaining accurate records of material movement and usage.
Storage optimization and proper material handling procedures have been shown to directly impact project timelines and budgets. The establishment of designated storage areas, implementation of FIFO systems, and proper protection of materials from environmental factors can lead to substantial cost savings and reduced material deterioration.
Supply chain integration remains a critical component of successful material management. By fostering strong relationships with suppliers and maintaining clear communication channels, construction companies can better anticipate delivery schedules, manage inventory levels, and respond effectively to material shortages or delays.
Sustainability considerations have become increasingly important in construction material management. The adoption of recycling programs, waste reduction strategies, and environmentally conscious material selection demonstrates commitment to environmental stewardship while often resulting in cost benefits.
To implement these practices effectively, construction professionals should:
– Conduct regular audits of material management systems
– Invest in appropriate technology solutions for inventory tracking
– Train staff in proper material handling procedures
– Develop clear communication protocols with suppliers
– Establish measurable sustainability goals
– Regular review and update of material management policies
Success in construction site material management requires continuous improvement and adaptation to new technologies and methodologies. By focusing on these key areas and maintaining a systematic approach to material management, construction companies can achieve better project outcomes, reduced costs, and improved sustainability performance.
The future of construction material management lies in the integration of smart technologies, sustainable practices, and efficient processes. Companies that embrace these elements while maintaining focus on practical implementation will be better positioned for success in an increasingly competitive industry.