Revolutionary construction technologies are transforming the building industry, driving unprecedented levels of efficiency, safety, and sustainability. With recent construction technology funding reaching historic levels, innovative solutions like Building Information Modeling (BIM), autonomous equipment, and advanced materials are becoming industry standards rather than exceptions.
From AI-powered project management platforms that reduce planning time by 40% to drone-based site surveillance that cuts inspection costs by half, these technologies are delivering measurable improvements across the construction lifecycle. Prefabrication and modular construction techniques, enhanced by robotics and 3D printing, are achieving 30% faster project completion while maintaining superior quality control.
Leading construction firms implementing these technologies report significant advantages: 25% reduction in project delays, 20% decrease in material waste, and up to 35% improvement in worker safety metrics. As the industry continues its digital transformation, understanding and adopting these technological innovations has become crucial for maintaining competitive advantage and meeting increasingly complex project demands.
Digital Twin Technology Revolutionizes Project Planning
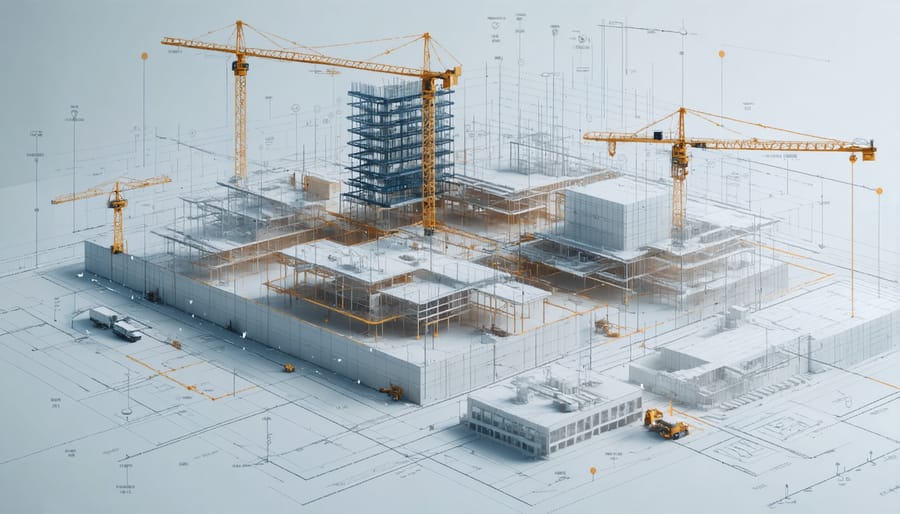
Real-time Project Monitoring
Digital twins are revolutionizing project monitoring by creating virtual replicas of construction sites that update in real-time. These sophisticated 3D models integrate data from IoT sensors, drones, and construction management software to provide comprehensive site visibility and predictive insights.
Project managers can monitor multiple aspects simultaneously, including equipment performance, material usage, worker productivity, and safety compliance. Sensors deployed across the site continuously transmit data about structural integrity, environmental conditions, and equipment status, enabling immediate response to potential issues before they escalate.
The predictive maintenance capabilities of digital twins are particularly valuable for large-scale projects. By analyzing patterns in equipment performance data, the system can forecast maintenance needs and prevent costly breakdowns. This proactive approach typically reduces maintenance costs by 15-25% and extends equipment life by 20%.
Real-world implementation at major construction sites has demonstrated significant improvements in project efficiency. For instance, a recent high-rise development project reported a 30% reduction in unexpected delays and a 25% improvement in resource utilization after implementing digital twin technology for real-time monitoring.
Risk Assessment and Mitigation
Digital twins have revolutionized risk assessment in construction by creating virtual replicas of physical structures and processes. These sophisticated 3D models enable project teams to simulate various scenarios and identify potential hazards before they materialize on-site. By integrating real-time data from IoT sensors and project management systems, digital twins provide continuous monitoring of structural integrity, environmental conditions, and operational parameters.
Project managers can analyze multiple risk factors simultaneously, from structural stress points to weather impacts, while also addressing construction cybersecurity risks associated with connected systems. The technology enables teams to run “what-if” scenarios, testing different construction sequences and identifying optimal solutions that minimize both safety risks and project delays.
This proactive approach to risk mitigation has proven particularly valuable in complex urban projects, where teams can visualize and plan for potential conflicts with existing infrastructure, traffic patterns, and neighboring structures. The resulting data-driven insights help stakeholders make informed decisions about resource allocation, safety protocols, and contingency planning, ultimately leading to safer, more efficient construction processes.
Robotics and Automation in Construction
Autonomous Construction Equipment
Autonomous construction equipment represents a significant advancement in construction automation, utilizing sophisticated AI, GPS, and sensor technologies to perform tasks with minimal human intervention. These self-operating machines include excavators, bulldozers, and material handlers that can execute precise earthmoving operations, grade sites, and transport materials across job sites with exceptional accuracy.
The technology employs a combination of LiDAR sensors, cameras, and sophisticated positioning systems to create real-time 3D maps of the construction environment. This enables the equipment to navigate complex terrains while avoiding obstacles and maintaining safety protocols. Leading manufacturers have developed systems capable of performing repetitive tasks with consistency that surpasses human operators, reducing errors and improving productivity by up to 30%.
Recent implementations have demonstrated success in large-scale infrastructure projects, where autonomous dozers and excavators work in coordination to prepare sites and maintain precise grading specifications. The technology has proven particularly valuable in hazardous environments and remote locations, where human operator safety is a concern.
While fully autonomous operation is still evolving, semi-autonomous features are becoming standard in modern construction equipment, offering features like automated blade control, bucket positioning, and machine guidance systems that enhance operator efficiency and project outcomes.
3D Printing in Construction
Large-scale 3D printing technology is revolutionizing construction by enabling the rapid fabrication of building components and entire structures with unprecedented precision and efficiency. This technology utilizes specialized concrete mixtures and computer-controlled robotic arms to deposit material layer by layer, creating complex geometric shapes and structures that would be challenging to achieve through traditional construction methods.
Leading construction firms are implementing 3D printing to fabricate structural elements, walls, and even complete buildings. The technology reduces labor costs by up to 80% and construction time by 60% compared to conventional methods. Notable examples include the world’s first 3D-printed office building in Dubai and residential developments in the Netherlands featuring custom-designed homes produced through additive manufacturing.
The advantages extend beyond speed and cost savings. 3D printing minimizes material waste, reduces environmental impact, and allows for greater design flexibility. Construction companies can create optimized structural components that use less material while maintaining structural integrity. The technology also enables on-site printing, reducing transportation costs and logistical complexities.
Recent developments include improved concrete formulations specifically designed for 3D printing, enhanced printing precision, and the ability to incorporate multiple materials within a single print. These advancements are making the technology increasingly viable for mainstream construction applications.
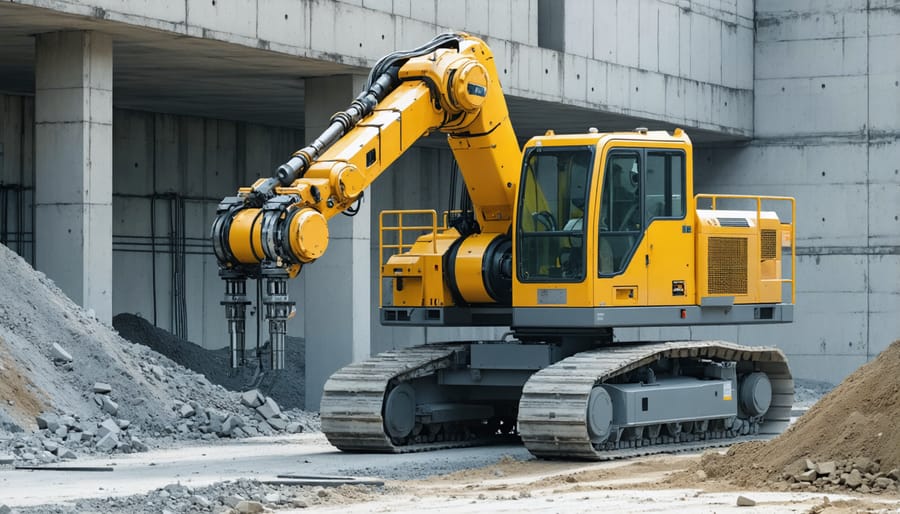
AI and Machine Learning Applications
Predictive Analytics for Project Management
Predictive analytics powered by artificial intelligence is revolutionizing construction project management by enabling data-driven decision-making and accurate forecasting. Advanced algorithms analyze historical project data, weather patterns, resource allocation records, and performance metrics to generate precise predictions for project timelines and resource requirements.
These AI systems can identify potential bottlenecks, assess risk factors, and recommend optimal resource distribution across different project phases. For example, machine learning models can predict labor needs based on project complexity, site conditions, and seasonal variations, helping managers optimize workforce scheduling and reduce costly overruns.
Real-time data integration from IoT sensors and project management platforms allows these systems to continuously refine their predictions. Construction firms using predictive analytics report up to 25% improvement in project delivery times and 20% reduction in resource waste. The technology also enhances cash flow management by accurately forecasting material requirements and equipment utilization.
Leading construction companies are now implementing these tools to create dynamic project schedules that automatically adjust to changing conditions, ensuring more reliable project completion estimates and better stakeholder communication.
Safety Monitoring Systems
Modern construction sites are increasingly adopting AI-powered safety monitoring systems to prevent accidents and enhance workplace security. These sophisticated platforms utilize a network of IoT sensors, cameras, and wearable devices to provide real-time monitoring of site conditions and worker activities.
Smart hard hats equipped with sensors track worker location, detect falls, and monitor vital signs, while AI-enabled cameras analyze site activities to identify potential safety violations. Machine learning algorithms process this data to predict hazardous situations before they occur, enabling proactive risk management.
According to industry data, construction sites implementing these systems have reported up to 45% reduction in workplace incidents. For instance, Skanska USA deployed an AI safety monitoring system across their projects, resulting in a 30% decrease in reportable incidents within the first year.
These systems also facilitate compliance monitoring by automatically documenting safety violations and generating detailed reports. Advanced features include proximity detection to prevent collisions between workers and heavy machinery, environmental monitoring for hazardous conditions, and automated emergency response protocols. The integration of these technologies demonstrates the industry’s commitment to creating safer work environments through technological innovation.
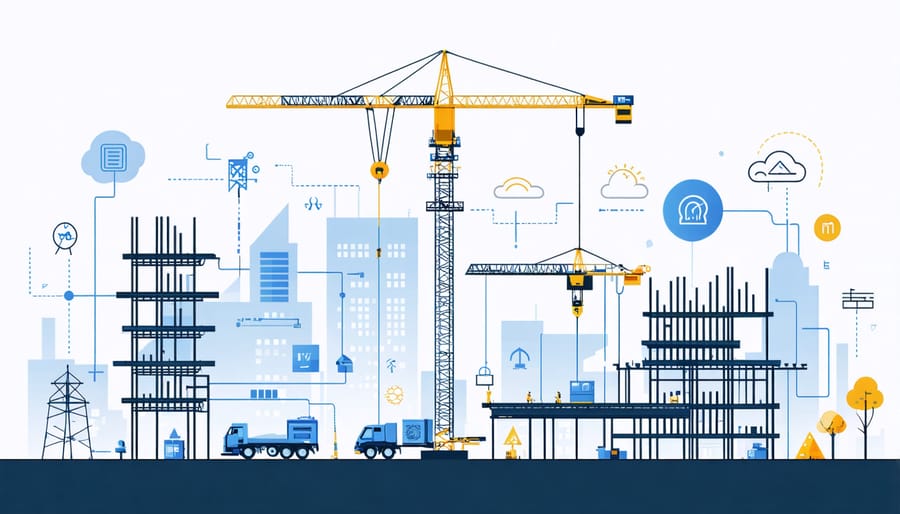
Smart Materials and IoT Integration
The integration of smart materials and Internet of Things (IoT) technology is transforming modern construction practices, creating buildings that are more responsive, efficient, and sustainable. Advanced composite materials, such as self-healing concrete embedded with bacteria that activate when cracks form, are revolutionizing structural durability and maintenance requirements. These innovations represent a significant leap forward in smart building innovations that reduce lifecycle costs.
IoT sensors are being strategically implemented throughout structures to monitor various parameters in real-time. Temperature, humidity, occupancy, and structural stress sensors provide continuous data streams that enable predictive maintenance and optimal building performance. Phase-changing materials (PCMs) integrated into building envelopes actively respond to environmental conditions, helping regulate internal temperatures and reduce energy consumption.
Recent developments include photochromic glass that automatically adjusts its transparency based on sunlight intensity, and piezoelectric materials that convert mechanical stress into electrical energy. These materials work in conjunction with IoT networks to create adaptive environments that respond to occupant needs while maximizing energy efficiency.
The implementation of smart dust sensors – microscopic IoT devices – allows for unprecedented monitoring of building conditions. These tiny sensors can detect everything from air quality to structural integrity, creating a comprehensive digital nervous system throughout the building. When combined with AI-powered building management systems, this sensor network enables autonomous adjustment of building systems, ensuring optimal performance while minimizing human intervention.
Industry leaders are particularly focused on developing smart materials that enhance both sustainability and resilience. Carbon-absorbing surfaces, self-cleaning coatings, and energy-harvesting materials are becoming increasingly common in forward-thinking construction projects.
The rapid evolution of construction technologies continues to reshape the industry landscape, driving unprecedented efficiencies and innovations. From AI-powered project management to advanced robotics and sustainable construction technologies, these advancements are fundamentally transforming how we build. As we look ahead, the integration of digital twins, automation, and smart materials promises even greater possibilities for enhanced productivity, safety, and sustainability. Industry leaders who embrace these technological innovations will be better positioned to address growing urbanization challenges, labor shortages, and environmental concerns. The future of construction clearly lies in the continued adoption and refinement of these transformative technologies, marking an exciting era of digital transformation and sustainable development in the built environment.