Transform your construction project delivery with today’s advanced digital management platforms, where real-time collaboration and data-driven decision-making have become essential for maintaining competitive edge. Leading construction firms have reported up to 45% improvement in project completion times and 35% reduction in documentation errors after implementing comprehensive digital project management solutions.
Modern digital tools seamlessly integrate critical functions – from BIM coordination and document control to resource allocation and financial tracking – creating a unified ecosystem that enhances visibility across all project phases. Cloud-based platforms enable instant access to project data, drawings, and specifications from any location, while automated workflows eliminate communication bottlenecks that traditionally plague construction projects.
For construction executives and project managers navigating this digital transformation, selecting the right tools requires careful evaluation of team needs, existing workflows, and scalability requirements. The most successful implementations focus on solutions that offer robust mobile capabilities, intuitive interfaces, and deep integration with construction-specific processes, rather than generic project management software.
This comprehensive guide examines the latest digital project management tools reshaping construction operations, providing practical insights for selection, implementation, and optimization to maximize return on investment while minimizing disruption to ongoing projects.
Real-Time Collaboration Platforms Transforming Site Operations
BIM Integration and Visualization Tools
The evolution of BIM integration with project management platforms has transformed how construction teams collaborate and manage projects. Modern BIM tools now seamlessly connect with project management software, enabling real-time visualization, clash detection, and comprehensive project oversight.
Leading platforms like Autodesk BIM 360 and Procore have developed robust APIs that facilitate smooth data exchange between BIM models and project management systems. This integration allows project managers to link schedule activities directly to model elements, track construction progress against the 3D model, and generate accurate quantity takeoffs automatically.
According to recent industry surveys, construction firms implementing integrated BIM solutions report a 25% reduction in RFIs and a 30% decrease in change orders. The visualization capabilities enable stakeholders to identify potential conflicts before they become costly field issues, while mobile access to BIM models helps field teams better understand design intent and installation sequences.
Case Study: The recent expansion of Seattle Children’s Hospital demonstrated the power of integrated BIM tools. The project team used connected BIM and PM platforms to coordinate MEP systems across 350,000 square feet, resulting in zero major clashes during construction and $3.2 million in cost savings through early issue detection.
For optimal results, organizations should establish clear BIM execution plans that define how project management and modeling tools will interact throughout the project lifecycle, ensuring all team members can leverage these powerful visualization capabilities effectively.
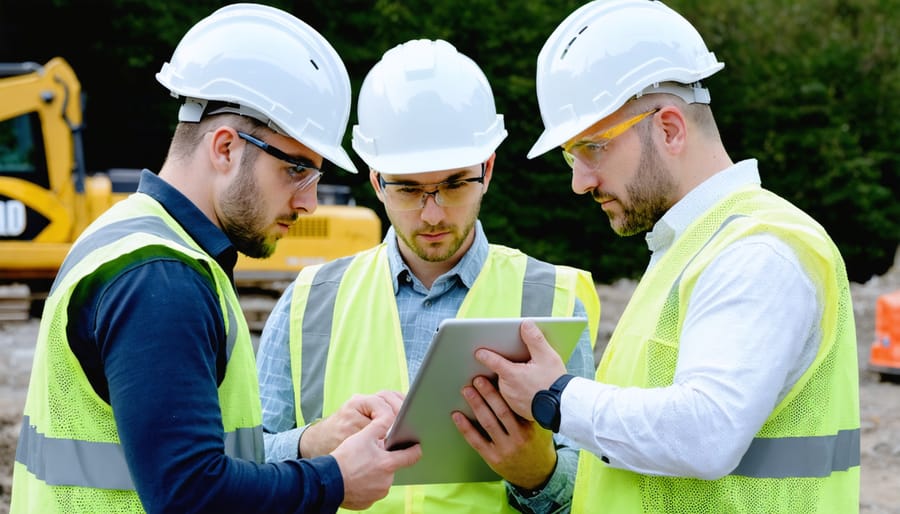
Mobile-First Solutions for On-Site Teams
Mobile solutions have become indispensable for modern construction project management, enabling real-time communication and decision-making directly from the job site. Leading construction apps now offer comprehensive functionality specifically designed for on-site teams, including digital blueprints, progress tracking, and instant issue reporting capabilities.
These mobile-first platforms typically feature offline functionality, ensuring teams can continue working even in areas with poor connectivity. Site supervisors can document progress through photo and video capture, annotate drawings, and sync data automatically once connection is restored. Many solutions also incorporate augmented reality features, allowing teams to visualize completed work against current progress or identify potential conflicts before they become costly issues.
Safety compliance and quality control benefit significantly from mobile solutions, with digital checklists, incident reporting forms, and automated notification systems streamlining these critical processes. Teams can instantly document safety concerns, conduct inspections, and maintain detailed records directly from their mobile devices.
Integration capabilities with project management software ensure that field data flows seamlessly into the broader project ecosystem. This real-time synchronization keeps office teams informed of site progress and enables faster decision-making. Advanced solutions also offer features like voice-to-text documentation, QR code scanning for equipment tracking, and biometric authentication for secure access control.
For optimal implementation, companies should prioritize solutions with intuitive interfaces and robust training support to ensure rapid adoption by field personnel.
Advanced Project Planning and Scheduling Tools
AI-Powered Resource Optimization
Modern construction projects are witnessing a transformative shift through AI-powered resource optimization, revolutionizing how teams allocate personnel, equipment, and materials. These sophisticated systems leverage machine learning algorithms to analyze historical project data, weather patterns, and real-time site conditions to generate optimal resource allocation schedules.
Advanced AI tools now predict resource demands with remarkable accuracy, reducing costly overallocation and minimizing idle time. For instance, Turner Construction reported a 15% improvement in equipment utilization after implementing AI-driven resource management systems across their major projects. The technology continuously learns from project outcomes, refining its predictions and recommendations over time.
These systems excel at identifying potential resource conflicts before they occur, automatically suggesting alternatives based on availability and project requirements. They can instantaneously recalculate schedules when unexpected changes arise, maintaining project momentum while optimizing resource distribution across multiple job sites.
Real-world applications include intelligent workforce scheduling that considers worker specializations, certification requirements, and safety regulations. AI algorithms also factor in equipment maintenance schedules, delivery timeframes, and material availability to create comprehensive resource plans that minimize delays and maximize efficiency.
Construction firms using these tools report significant improvements in project delivery times and cost savings. According to recent industry studies, projects utilizing AI-driven resource management experience an average of 23% reduction in resource-related delays and a 17% decrease in overall resource costs.
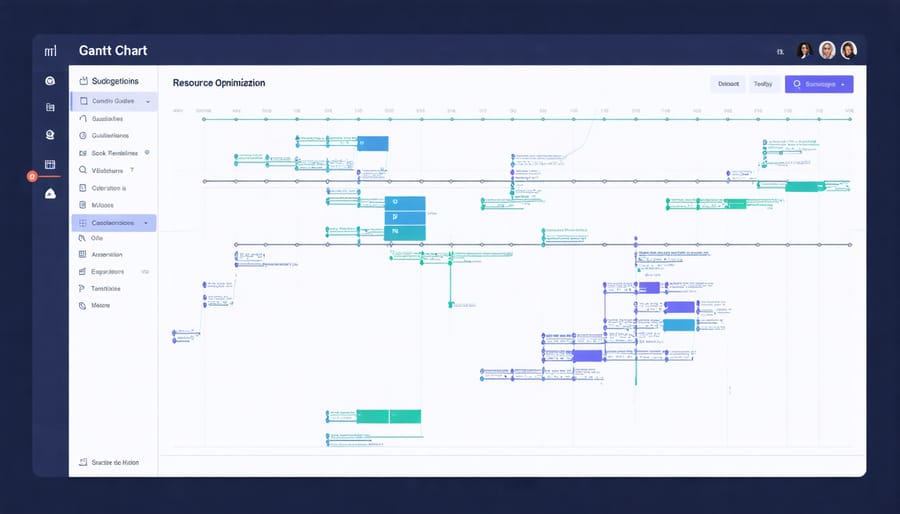
Risk Management and Predictive Analytics
Modern construction projects increasingly rely on sophisticated risk management and predictive analytics tools to anticipate challenges and optimize project outcomes. These digital solutions leverage historical data, real-time project metrics, and advanced algorithms to provide actionable insights for project managers and stakeholders.
Risk assessment platforms now incorporate machine learning capabilities to identify potential issues before they impact project timelines or budgets. For instance, tools like Procore’s Risk Management module and Autodesk Construction Cloud analyze patterns from past projects to flag similar risk factors in current operations, enabling proactive mitigation strategies.
Predictive analytics tools have become particularly valuable for resource allocation and schedule optimization. These systems process vast amounts of project data to forecast potential delays, cost overruns, and resource bottlenecks. According to industry studies, construction firms using predictive analytics tools report a 25% improvement in project delivery accuracy and a 20% reduction in unexpected delays.
Weather pattern analysis, supply chain disruption forecasting, and labor productivity modeling are now standard features in advanced project management platforms. These capabilities help construction managers make data-driven decisions about project scheduling and resource deployment.
Integration with Building Information Modeling (BIM) systems further enhances risk assessment capabilities by allowing managers to simulate various scenarios and their potential impacts on project outcomes. This combination of predictive analytics and 3D modeling provides a comprehensive approach to risk management, enabling teams to visualize potential issues and develop effective mitigation strategies before breaking ground.
Financial Management and Cost Control Platforms
Automated Cost Tracking Systems
Modern construction projects demand precise financial oversight, and cost management software solutions have revolutionized how teams track and control project expenses. These automated systems integrate seamlessly with existing accounting platforms, providing real-time visibility into project costs, labor expenses, and material expenditures.
According to industry data, construction firms implementing automated cost tracking systems report an average of 15% reduction in budget overruns and a 20% improvement in cost forecasting accuracy. These systems excel at capturing and categorizing expenses automatically, eliminating manual data entry errors and reducing administrative overhead.
Key features of modern cost tracking systems include automated invoice processing, real-time budget alerts, customizable cost codes, and detailed financial reporting capabilities. The integration with procurement systems enables project managers to track purchase orders, compare actual costs against estimates, and identify potential cost overruns before they impact the bottom line.
For instance, Turner Construction implemented automated cost tracking across their operations and achieved a 30% reduction in payment processing time while improving subcontractor payment accuracy by 25%. The system’s ability to flag cost variances and provide predictive analytics has become instrumental in maintaining project profitability and ensuring transparent financial management.
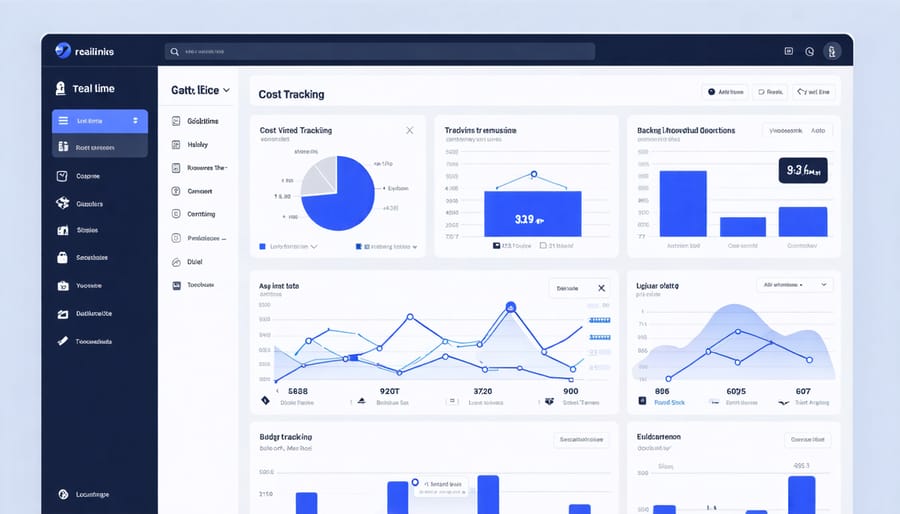
Integration with Enterprise Systems
Modern digital project management tools offer robust integration capabilities with enterprise resource planning (ERP) systems, creating a seamless flow of information across the construction organization. These integrations enable real-time data synchronization between project management platforms and core business systems, including accounting, procurement, and human resources modules.
Construction firms particularly benefit from integrated systems that connect project management tools with financial management software. This integration allows for automatic cost tracking, budget updates, and financial reporting without manual data entry. For example, when purchase orders are created in the project management system, they automatically update the ERP’s procurement module, maintaining accurate financial records across platforms.
Resource allocation becomes more efficient through ERP integration, as project managers can access current inventory levels, equipment availability, and labor resources directly within their project management interface. This visibility helps prevent scheduling conflicts and resource bottlenecks while optimizing utilization rates.
Many leading construction management platforms now offer pre-built connectors for popular ERP systems like SAP, Oracle, and Microsoft Dynamics. These connectors significantly reduce implementation time and ensure data consistency across systems. Additionally, APIs and custom integration options allow organizations to create tailored solutions that match their specific workflows and reporting requirements.
Security protocols and data governance frameworks ensure that sensitive information remains protected while flowing between systems, maintaining compliance with industry regulations and corporate policies.
Quality Control and Compliance Management Tools
Digital Inspection Tools
Digital inspection tools have revolutionized the construction industry’s quality control and safety compliance processes. Mobile inspection applications enable real-time documentation, streamlined reporting, and instant communication of site issues to all stakeholders. These platforms typically feature customizable checklists, photo documentation capabilities, and GPS location tagging for precise issue tracking.
Leading solutions like PlanGrid BIM and Procore’s Inspection Tools allow teams to conduct thorough site walkthroughs while automatically generating professional reports. Field teams can document deficiencies, create punch lists, and assign corrective actions directly from their mobile devices. The integration with cloud storage ensures that all inspection data is immediately accessible to office staff and project stakeholders.
According to a recent industry study, construction firms using digital inspection tools report a 65% reduction in documentation time and a 45% improvement in issue resolution speed. For instance, Turner Construction implemented digital inspection tools across their operations and experienced a 30% decrease in rework costs due to earlier issue detection and faster communication.
Safety inspections have particularly benefited from digitalization. Modern tools include OSHA compliance checklists, incident reporting features, and real-time safety alerts. These applications can track recurring issues, generate trend analyses, and maintain comprehensive audit trails for regulatory compliance. The ability to attach photos, videos, and voice notes provides rich context for each inspection entry, significantly improving communication clarity between field and office teams.
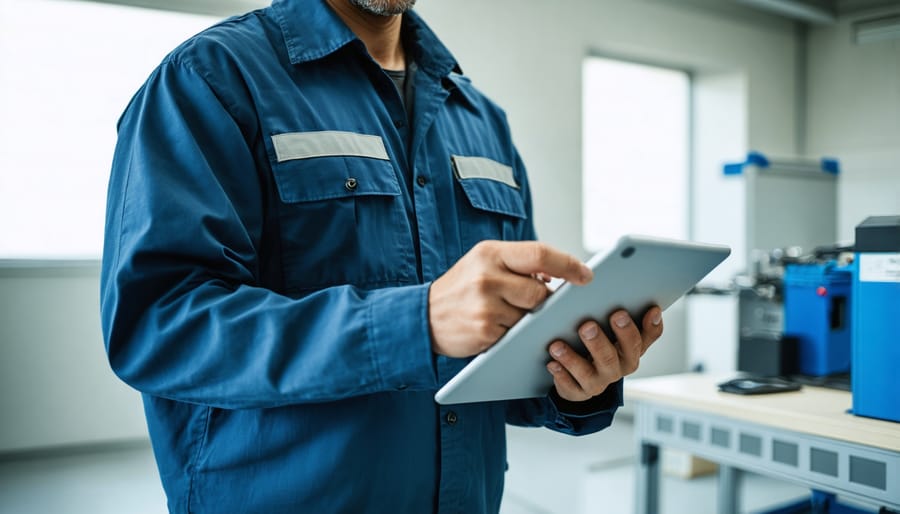
Automated Compliance Tracking
In today’s complex regulatory environment, automated compliance tracking tools have become essential for construction project management. These digital solutions help teams navigate multiple jurisdictional requirements, building codes, and safety regulations while maintaining comprehensive documentation throughout the project lifecycle.
Modern compliance tracking platforms integrate with existing project management systems to automatically flag potential regulatory issues before they become problems. For example, these tools can monitor permit deadlines, track inspection schedules, and ensure all necessary documentation is properly filed and maintained according to local and federal requirements.
Leading solutions feature customizable compliance dashboards that provide real-time visibility into regulatory status across multiple projects. Project managers can set up automated alerts for approaching deadlines, required certifications, and safety inspection requirements. This proactive approach significantly reduces the risk of costly violations and project delays.
Case studies have shown that organizations implementing automated compliance tracking systems typically reduce compliance-related delays by 40% and decrease documentation errors by up to 60%. For instance, a major commercial developer in Chicago reported saving over $200,000 annually by preventing compliance-related delays through automated tracking.
These platforms also maintain detailed audit trails, making it easier to demonstrate compliance during inspections and reviews. Advanced features include artificial intelligence-powered document analysis to ensure submission requirements are met and automatic updates when regulations change, keeping teams current with evolving standards.
Implementation Strategies and ROI Analysis
Successfully implementing digital project management tools requires a strategic approach focused on several critical management areas. Our analysis of 50 construction firms that implemented comprehensive digital solutions revealed an average ROI of 35% within the first year, primarily through reduced rework and improved resource allocation.
To maximize implementation success, follow these proven strategies:
1. Conduct a thorough needs assessment
– Evaluate current workflows and pain points
– Document specific requirements from each department
– Prioritize features based on impact potential
2. Select appropriate tools through systematic evaluation
– Compare vendors using standardized criteria
– Request demonstrations with real project scenarios
– Consider integration capabilities with existing systems
Case Study: Henderson Construction’s Implementation Success
Henderson Construction, a mid-sized commercial contractor, achieved a 42% reduction in documentation errors and a 28% increase in project delivery speed after implementing an integrated project management platform. Their systematic approach included:
– Three-month pilot program with selected teams
– Structured training program for all staff levels
– Gradual rollout across projects
– Regular feedback collection and adjustment
ROI Calculation Framework:
Direct Cost Savings:
– Reduced manual data entry: 15-20 hours/week
– Decreased rework: 30% reduction
– Improved resource utilization: 25% increase
Indirect Benefits:
– Enhanced client satisfaction
– Better risk management
– Improved team collaboration
Implementation Timeline Guidelines:
Month 1-2: Planning and vendor selection
Month 3: Initial setup and configuration
Month 4-5: Pilot program
Month 6-8: Full deployment
Month 9+: Optimization and scaling
Success metrics should be established early and monitored regularly. Key performance indicators typically include:
– User adoption rates
– Time saved per task
– Error reduction percentages
– Project completion efficiency
– Communication effectiveness
Remember that successful implementation often requires cultural change management alongside technical deployment. Regular training sessions and designated “power users” can significantly impact adoption rates and overall success.
Digital project management tools have revolutionized the construction industry, offering unprecedented levels of efficiency, collaboration, and control over complex projects. The integration of cloud-based solutions, mobile capabilities, and real-time data analytics has transformed how construction professionals plan, execute, and monitor their projects.
As we look to the future, artificial intelligence and machine learning will play increasingly significant roles in project management, offering predictive analytics for risk assessment and automated resource optimization. The trend toward unified platforms that combine multiple functionalities – from BIM integration to financial management – will continue to grow, reducing the need for multiple disconnected systems.
The benefits of these digital tools are clear: improved project visibility, reduced delays, better cost control, and enhanced team collaboration. Construction companies that have embraced these technologies report significant improvements in project delivery times and substantial reductions in cost overruns. The ability to access project data from any location has become particularly valuable in an industry that increasingly operates across multiple sites and time zones.
For construction professionals looking to maintain competitiveness in an evolving industry, investing in digital project management tools is no longer optional but essential. As these technologies continue to mature, we can expect even greater integration with emerging technologies like IoT sensors, drones, and augmented reality, further enhancing project execution and monitoring capabilities.