Dubai’s pioneering efforts in 3D-printed construction have revolutionized the building industry, positioning the emirate at the forefront of architectural construction innovations. In 2016, the city unveiled the world’s first 3D-printed office building, and since then, has committed to an ambitious target: constructing 25% of all new buildings using 3D printing technology by 2030.
This transformative approach has reduced construction costs by 50-70%, shortened project timelines by up to 70%, and minimized waste materials by 60% compared to traditional building methods. Through strategic partnerships with leading technology providers and implementation of strict regulatory frameworks, Dubai has created a robust ecosystem for 3D-printed construction that sets new global standards for efficiency and sustainability.
The integration of advanced robotics, specialized concrete mixtures, and sophisticated digital modeling has enabled the creation of complex architectural designs while maintaining structural integrity and meeting stringent building codes. This technological leap forward represents not just an evolution in construction methodology, but a complete paradigm shift in how we approach urban development and architectural design.
Dubai’s Strategic 3D Printing Initiative
The Dubai 3D Printing Strategy
The Dubai 3D Printing Strategy, launched in 2016 by Sheikh Mohammed bin Rashid Al Maktoum, represents one of the most ambitious construction initiatives globally. The strategy’s cornerstone target aims to have 25% of all new buildings in Dubai constructed using 3D printing technology by 2030, positioning the emirate as a global hub for 3D printing construction innovation.
This comprehensive strategy encompasses three major sectors: construction, medical products, and consumer products, with construction playing the pivotal role. The initiative is expected to reduce construction costs by 50-70%, cut labor requirements by 50-80%, and significantly decrease construction waste, aligning with Dubai’s sustainability goals.
The strategy is supported by robust regulatory frameworks and strategic partnerships with technology providers, research institutions, and construction companies. The Dubai Municipality has implemented specialized building codes and regulations specifically for 3D-printed structures, ensuring safety and quality standards while facilitating innovation.
To achieve its 2030 target, Dubai has established a detailed roadmap including workforce development programs, research funding, and incentives for construction companies adopting 3D printing technology. The strategy also emphasizes developing local expertise and manufacturing capabilities to create a sustainable 3D printing ecosystem.
Regulatory Framework and Standards
Dubai has established itself as a pioneer in regulating 3D printing construction, implementing comprehensive frameworks that balance innovation with safety and quality standards. In 2016, the Dubai Municipality introduced the first specialized regulations for 3D printed buildings, making it one of the first cities globally to create such guidelines.
The regulatory framework mandates specific requirements for materials, structural integrity, and construction methodologies. All 3D printed structures must undergo rigorous testing and certification processes, including material strength assessments and structural analysis. The regulations also specify minimum durability standards and environmental performance criteria.
Key aspects of Dubai’s 3D printing construction regulations include mandatory use of approved printing materials, specific requirements for reinforcement integration, and detailed guidelines for quality control during the printing process. Projects must also comply with Dubai’s existing building codes while incorporating specialized provisions for additive manufacturing techniques.
Contractors and developers must obtain specific permits and certifications before undertaking 3D printed construction projects, ensuring that all stakeholders maintain high safety and quality standards throughout the construction process.
Landmark 3D Printed Projects in Dubai
The Office of the Future
Dubai’s pioneering venture into 3D-printed architecture materialized in 2016 with the completion of the “Office of the Future,” marking a significant milestone in construction innovation. Located in the Emirates Towers premises, this 2,700-square-foot structure represents the world’s first fully functional 3D-printed office building.
The project, executed by WinSun Global in collaboration with Dubai Municipality, demonstrated remarkable efficiency in construction. The entire printing process took merely 17 days, followed by two days of installation on site. This achievement represented a 50% reduction in labor costs and generated 60% less construction waste compared to traditional building methods.
The office building’s structural components were printed using a specialized cement mixture, reinforced with fiber materials to ensure durability and structural integrity. The printer, measuring 20 feet high, 120 feet long, and 40 feet wide, operated with precision to create the building’s components in a controlled factory environment.
The interior design prioritizes functionality while showcasing the aesthetic possibilities of 3D printing technology. Features include open-plan workspaces, meeting rooms, and innovative architectural elements that would be challenging to achieve through conventional construction methods.
Beyond its architectural significance, the Office of the Future serves as a testing ground for future 3D-printed structures in Dubai. The building’s performance is continuously monitored for structural behavior, sustainability metrics, and operational efficiency, providing valuable data for future projects. This initiative aligns with Dubai’s ambitious strategy to have 25% of all new buildings 3D-printed by 2030, demonstrating the emirate’s commitment to advancing construction technology.
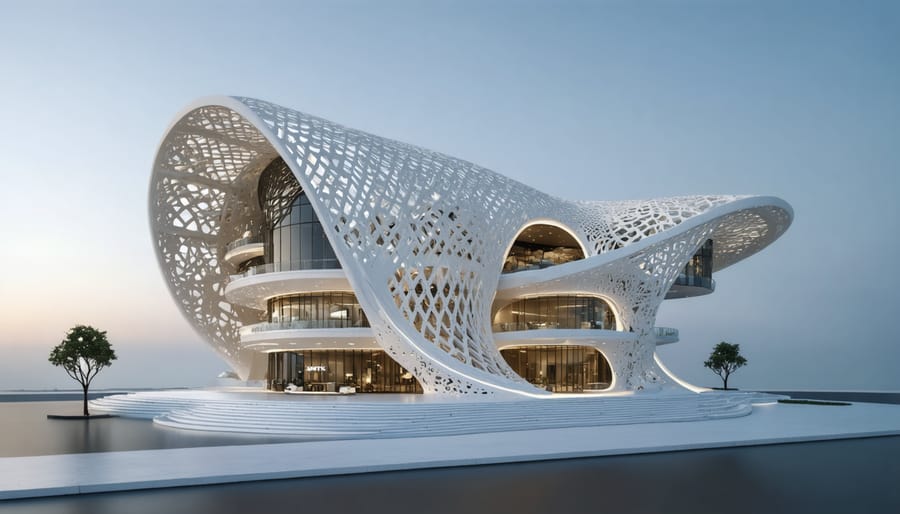
Current Construction Projects
Dubai’s 3D printing construction landscape is currently experiencing unprecedented growth, with several groundbreaking projects underway across the emirate. The Dubai Municipality’s ambitious “3D Printing Strategic Alliance” initiative has catalyzed multiple developments, including the construction of a three-story government administrative building in Warqaa area, set to become the largest 3D-printed structure in the region upon completion in late 2024.
In Dubai South, construction firm MEET is executing a residential complex comprising 14 townhouses, utilizing advanced robotic 3D printing technology. The project showcases the integration of traditional construction methods with automated printing processes, promising completion 70% faster than conventional building methods.
The Dubai Future Foundation’s “Office of the Future” expansion project is another notable development, adding two additional wings to the existing structure. This project incorporates enhanced concrete mixtures specifically engineered for Dubai’s climate conditions, addressing previous challenges with material durability and thermal performance.
At Dubai Industrial City, tech company CyBe Construction has begun work on a 2,000-square-meter industrial facility, demonstrating the scalability of 3D printing technology for larger commercial applications. The project utilizes a mobile printing system capable of operating in temperatures up to 45°C, specifically adapted for Dubai’s environmental conditions.
Additionally, DEWA’s Research & Development Center is overseeing the construction of several pilot projects, including a series of sustainable villas in Hatta, which combine 3D printing technology with solar power integration and smart home systems. These projects align with Dubai’s commitment to achieving 25% 3D-printed buildings by 2030, showcasing the emirate’s position as a global leader in construction innovation.
Technical Innovation and Implementation
Construction Technology and Materials
Dubai’s pioneering 3D printing construction projects utilize state-of-the-art gantry-based systems and robotic arm printers, representing the latest in advanced building systems. These systems employ precision-controlled nozzles that extrude specialized concrete mixtures layer by layer, achieving unprecedented accuracy within 1mm tolerance.
The proprietary concrete formulations used in Dubai’s 3D printing projects are among the most sophisticated next-generation building materials in construction. These mixes incorporate advanced polymers, fiber reinforcement, and specialized additives that ensure optimal flowability during printing while maintaining structural integrity. The material achieves 50-70% faster curing times compared to traditional concrete, with compressive strengths exceeding 50 MPa after 28 days.
The printing technology incorporates real-time monitoring systems that adjust material flow rates and printing speeds based on environmental conditions. Temperature-controlled printing chambers maintain optimal conditions for material deposition and curing, particularly crucial in Dubai’s challenging climate. The system’s automated quality control mechanisms continuously monitor layer adhesion, dimensional accuracy, and structural integrity throughout the printing process.
Recent developments include the integration of BIM-driven parametric design capabilities, allowing for automated adjustment of printing parameters based on architectural specifications and structural requirements. This ensures seamless translation from digital models to physical construction while maintaining strict quality standards.
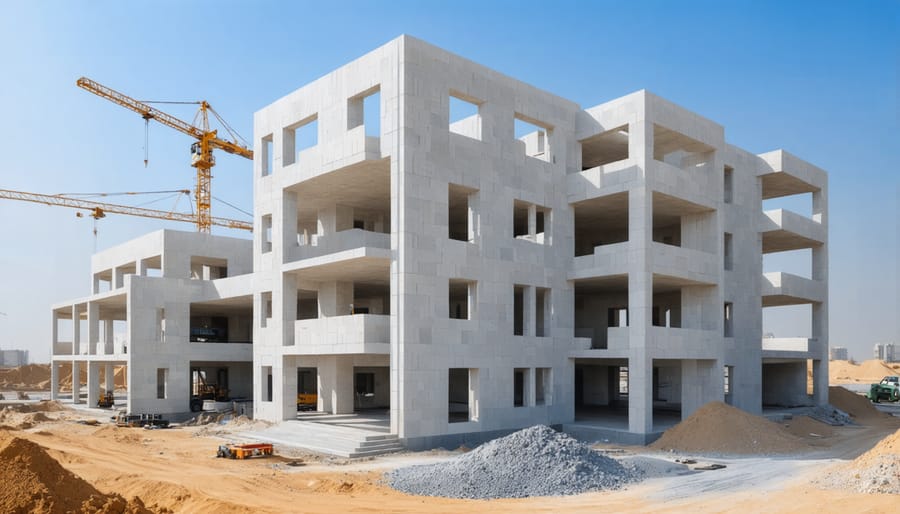
Construction Process and Efficiency
The construction process of Dubai’s 3D-printed buildings represents a significant departure from traditional methods, achieving remarkable efficiency gains. The process begins with a digital model, which is translated into machine instructions for the specialized concrete printer. Using a gantry-mounted printing head, the system deposits layers of proprietary cement mixture in precise patterns according to the architectural design.
Compared to conventional construction, 3D printing reduces labor requirements by up to 70% and cuts construction time by 50-70%. The technology eliminates the need for formwork and significantly reduces material waste, resulting in cost savings of 30-50%. The specialized concrete mixture, developed specifically for Dubai’s climate conditions, reaches optimal strength within 24 hours of printing.
The printing process operates continuously, requiring minimal human intervention beyond material supply and quality monitoring. A typical 2,000 square foot structure can be printed in just 48 hours, with finishing work completed within two weeks. This dramatic acceleration of the construction timeline has profound implications for project scheduling and resource allocation.
Quality control is maintained through integrated sensors that monitor material consistency, layer adhesion, and structural integrity throughout the printing process. The technology also allows for the incorporation of building services (electrical, plumbing, and HVAC) during the printing phase, further streamlining the construction sequence and reducing coordination complexities.
Economic and Environmental Impact
Cost Analysis and Labor Requirements
The implementation of 3D printing technology in Dubai’s construction projects has demonstrated significant cost advantages compared to traditional building methods. According to the Dubai Municipality’s data, construction costs have been reduced by 50-70% in pilot projects, while labor requirements have decreased by 50-80%. This dramatic shift represents a fundamental construction sector transformation in terms of resource allocation and project economics.
Financial analysis of recent 3D-printed structures in Dubai reveals substantial savings in material costs, with up to 60% reduction in construction waste and a 25-30% decrease in overall project duration. Labor costs have shown particularly noteworthy improvements, with specialized teams of 3-4 operators replacing traditional construction crews of 15-20 workers. This reduction in workforce requirements has led to an estimated 50% decrease in labor-related expenses.
However, the initial investment in 3D printing technology remains significant, with equipment costs ranging from $500,000 to $2 million, depending on the scale and sophistication of the system. Despite these upfront costs, ROI calculations indicate a break-even point within 18-24 months for companies maintaining regular project volumes. The reduction in insurance costs, worker compensation, and site safety requirements further enhances the financial benefits, making 3D printing an increasingly attractive option for Dubai’s construction industry.
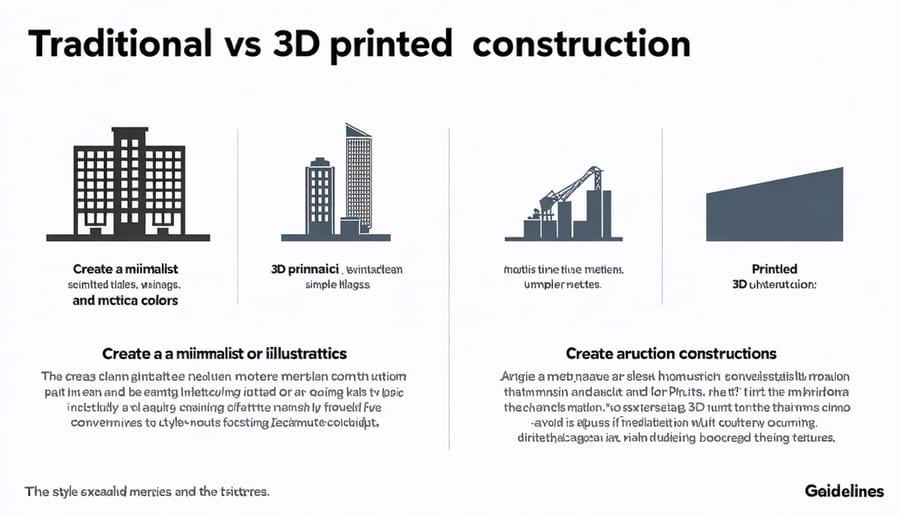
Environmental Benefits
Dubai’s 3D printing construction initiatives demonstrate significant environmental advantages over traditional building methods. Studies conducted by Dubai Municipality reveal that 3D-printed structures can reduce construction waste by up to 60%, addressing one of the industry’s most pressing environmental challenges. The precision of 3D printing technology ensures that materials are used only where needed, minimizing excess and optimizing resource utilization.
The reduced transportation requirements for 3D-printed buildings contribute substantially to lowering carbon emissions. With most materials mixed and prepared on-site, the number of vehicle movements decreases by approximately 40% compared to conventional construction methods. Additionally, the automated nature of 3D printing eliminates packaging waste associated with traditional building materials.
Concrete mixing for 3D printing is optimized through advanced algorithms, resulting in up to 30% less cement usage while maintaining structural integrity. This reduction is particularly significant given that cement production is a major contributor to global CO2 emissions. The technology also enables the incorporation of recycled materials and sustainable alternatives, including specialized eco-friendly concrete mixtures developed specifically for Dubai’s climate conditions.
The Dubai Municipality’s sustainability guidelines for 3D printing construction mandate the use of locally sourced materials where possible, further reducing the environmental impact through shortened supply chains. Energy consumption during construction is also notably lower, with estimates showing 20-30% reduction in overall energy usage compared to traditional building methods.
Dubai has firmly established itself as a global leader in 3D printed construction, demonstrating remarkable progress through strategic initiatives and groundbreaking projects. The emirate’s commitment to achieving its target of having 25% of all new buildings 3D printed by 2030 has catalyzed significant technological advancements and regulatory frameworks that serve as a model for other cities worldwide.
The successful completion of multiple 3D printed structures, including office buildings, residential villas, and specialized facilities, showcases the practical viability of this technology. These achievements have not only validated Dubai’s innovative approach but also created a robust ecosystem of manufacturers, technology providers, and construction professionals specialized in 3D printing construction.
Looking ahead, Dubai’s construction sector is poised for transformation as more developers adopt this technology. The continued investment in research and development, coupled with supportive regulations and training programs, indicates a strong foundation for future growth. The emirate’s experience demonstrates that 3D printing can significantly reduce construction costs, accelerate project timelines, and minimize environmental impact.
As Dubai continues to refine its expertise and expand its portfolio of 3D printed structures, it is setting new standards for sustainable and efficient construction practices. This pioneering approach positions Dubai as a knowledge hub for 3D printing construction technology, attracting international attention and investment while paving the way for widespread adoption across the global construction industry.