Maintaining EHS regulatory compliance in construction demands a strategic blend of proactive risk management, continuous monitoring, and unwavering commitment to safety standards. Recent industry data reveals that companies with robust EHS programs experience 70% fewer workplace incidents and save up to $4 for every $1 invested in safety protocols. Construction leaders must navigate an increasingly complex regulatory landscape while balancing productivity targets and workforce protection.
The stakes have never been higher, with OSHA penalties reaching up to $156,259 per violation in 2024, and heightened scrutiny on environmental impact and worker safety. Digital transformation has revolutionized compliance management, enabling real-time monitoring, automated reporting, and predictive risk assessment. Leading construction firms are leveraging integrated EHS management systems to streamline compliance processes, reduce administrative burden, and ensure consistent adherence to regulations across multiple project sites.
This comprehensive guide explores cutting-edge strategies for maintaining EHS compliance, incorporating advanced technologies, and fostering a culture of safety excellence. From implementing automated compliance tracking systems to developing comprehensive training programs, we’ll examine proven approaches that help construction companies not only meet regulatory requirements but exceed industry standards for safety and environmental stewardship.
Core EHS Compliance Requirements in Construction
OSHA Standards and Requirements
The Occupational Safety and Health Administration (OSHA) sets forth comprehensive OSHA construction regulations that form the backbone of workplace safety in the construction industry. These standards are primarily outlined in 29 CFR 1926, which addresses crucial areas including fall protection, scaffolding requirements, and electrical safety protocols.
Fall protection standards mandate that employers must provide protection systems for workers at heights of six feet or greater above lower levels. This includes guardrails, safety nets, or personal fall arrest systems. Scaffolding requirements specify that platforms must be fully planked, capable of supporting four times the maximum intended load, and equipped with appropriate guardrails and access points.
Electrical safety protocols require ground-fault circuit interrupters (GFCIs) for all temporary power on construction sites and proper lockout/tagout procedures during maintenance. Additionally, OSHA mandates comprehensive training programs for workers, maintaining detailed safety records, and regular workplace inspections.
Excavation and trenching standards require protective systems for trenches deeper than 5 feet, while crane operation regulations demand certification for operators and thorough equipment inspections. These requirements are complemented by mandatory hazard communication standards, ensuring workers are informed about potential chemical exposures and proper handling procedures.
Compliance with these standards isn’t merely about avoiding citations; it’s fundamental to maintaining a safe, productive workplace and protecting workers’ lives.
State and Local Compliance Considerations
While federal EHS regulations provide a baseline framework, state and local jurisdictions often impose additional requirements that construction professionals must navigate. These regional variations can significantly impact project planning and execution, requiring careful attention to compliance at multiple regulatory levels.
States like California, New York, and Massachusetts are known for implementing stricter EHS standards than federal requirements. For instance, California’s Cal/OSHA programs mandate more frequent safety inspections and detailed reporting procedures than federal OSHA guidelines. Local municipalities may further overlay specific requirements for noise control, dust management, and working hours.
Environmental regulations also vary considerably by region, particularly regarding waste disposal, water protection, and air quality standards. Urban areas typically enforce more stringent controls on construction activities that could affect public health or quality of life. For example, major cities often require detailed environmental impact assessments and specific mitigation measures before project approval.
To ensure comprehensive compliance, construction companies should:
– Maintain current knowledge of local regulations through regular consultation with authorities
– Develop region-specific compliance protocols
– Partner with local environmental consultants familiar with area requirements
– Establish clear communication channels with regulatory bodies
– Document all compliance efforts meticulously
Success in managing these varying requirements often depends on establishing strong relationships with local regulatory agencies and maintaining flexible compliance programs that can adapt to regional differences.
Implementing an Effective EHS Compliance Program
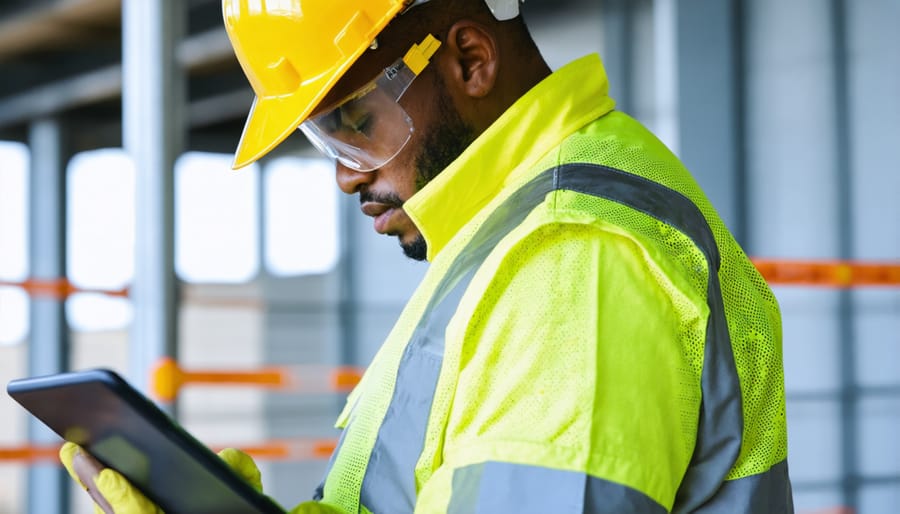
Risk Assessment and Management
Effective risk assessment and management form the cornerstone of EHS regulatory compliance in construction. The process begins with systematic hazard identification through comprehensive workplace inspections, analysis of historical incident data, and employee feedback mechanisms. Industry professionals should employ both qualitative and quantitative assessment methods to evaluate risks based on their likelihood and potential severity.
A structured approach to risk management typically involves implementing the hierarchy of controls: elimination, substitution, engineering controls, administrative controls, and personal protective equipment (PPE). Project managers must prioritize hazard elimination whenever feasible, followed by risk reduction through safer alternatives or engineering solutions.
Regular workplace monitoring and documentation are essential components of effective risk management. This includes maintaining detailed records of safety inspections, incident reports, and corrective actions taken. Modern digital tools and software solutions can streamline this process, enabling real-time hazard reporting and tracking of mitigation measures.
Construction companies should establish clear protocols for risk communication and emergency response. This includes developing written procedures, conducting regular safety briefings, and ensuring all workers understand their roles in maintaining workplace safety. Special attention should be paid to high-risk activities such as working at heights, confined space entry, and heavy equipment operation.
Success in risk management relies heavily on worker engagement and a strong safety culture. Regular training sessions, toolbox talks, and safety committees can help foster this culture while ensuring compliance with regulatory requirements.
Training and Documentation Requirements
Effective training programs and thorough documentation are cornerstones of EHS regulatory compliance in construction. Organizations must implement comprehensive training initiatives that cover critical safety standards and ensure all personnel understand their roles in maintaining workplace safety.
Training requirements typically include initial orientation for new employees, regular refresher courses, and specialized training for specific equipment or hazardous materials handling. Documentation must track completion dates, certification renewals, and competency assessments. Key training components should address:
• Hazard recognition and risk assessment
• Personal protective equipment (PPE) usage
• Emergency response procedures
• Equipment operation safety protocols
• Chemical handling and storage
• First aid and incident reporting
Organizations must maintain detailed records of:
• Training attendance and completion certificates
• Safety meeting minutes
• Incident reports and investigations
• Equipment inspection logs
• Safety audits and corrective actions
• Environmental monitoring results
Digital documentation systems are increasingly becoming standard practice, offering improved accessibility, automated renewal notifications, and simplified compliance reporting. These systems help organizations maintain up-to-date records while ensuring quick access during regulatory inspections or audits.
It’s essential to regularly review and update training materials to reflect changes in regulations, equipment, or procedures. This proactive approach helps maintain compliance while fostering a culture of continuous improvement in workplace safety.
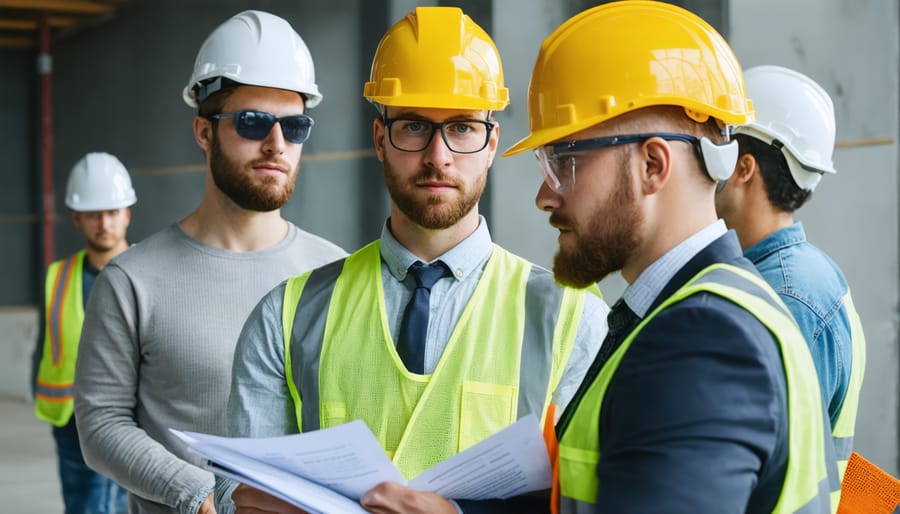
Monitoring and Enforcement Strategies
Effective monitoring and enforcement strategies form the backbone of successful EHS regulatory compliance in construction. Regular site audits and inspections should be conducted using standardized checklists that align with current regulations and company policies. These assessments should occur at predetermined intervals and after significant operational changes.
Digital monitoring systems have revolutionized compliance tracking, offering real-time data collection and analysis. Modern EHS management software enables automatic alerts for upcoming inspections, permit renewals, and training requirements. These platforms also facilitate immediate reporting of incidents or near-misses, allowing for swift corrective action.
Documentation plays a crucial role in enforcement. Maintain detailed records of all inspections, violations, corrective actions, and follow-up procedures. Implement a clear hierarchy of responsibility for addressing non-compliance issues, with specific timelines for resolution and accountability measures.
Establish a systematic approach to corrective actions through:
– Root cause analysis of violations
– Development of specific action plans
– Implementation timelines
– Follow-up verification procedures
– Documentation of outcomes
Employee engagement is essential for successful enforcement. Create a reporting system that encourages workers to identify potential compliance issues without fear of retaliation. Regular training sessions should reinforce compliance requirements and update staff on new regulations or procedures.
Consider implementing a metrics-based performance system that tracks compliance rates, response times to violations, and the effectiveness of corrective actions. This data-driven approach enables continuous improvement of your compliance program while demonstrating due diligence to regulatory authorities.
Technology and Tools for EHS Compliance
Digital Compliance Management Systems
Digital compliance management systems have revolutionized how construction companies handle EHS regulatory requirements. These sophisticated software solutions streamline compliance tracking, documentation, and reporting processes while reducing human error and increasing operational efficiency.
Modern compliance management platforms typically include features such as real-time monitoring dashboards, automated notification systems for upcoming deadlines, and centralized document repositories. These systems enable project managers to maintain digital records of safety inspections, training certifications, incident reports, and regulatory submissions in a secure, easily accessible format.
Key capabilities of these digital tools include:
– Automated compliance calendar management
– Mobile-friendly inspection checklists
– Incident tracking and investigation workflows
– Digital permit management
– Real-time reporting and analytics
– Integration with regulatory databases
Leading construction firms have reported significant improvements in compliance rates and reduced administrative burden after implementing these systems. For example, a major commercial builder decreased their compliance processing time by 60% and eliminated missed deadlines through automated alerts and standardized workflows.
When selecting a digital compliance management system, organizations should consider factors such as scalability, user interface simplicity, mobile accessibility, and integration capabilities with existing project management tools. Regular system updates ensure alignment with changing regulations and industry standards, while cloud-based solutions offer the advantage of remote access and improved collaboration among team members.
Mobile Applications and Real-time Monitoring
Mobile applications and real-time monitoring tools have revolutionized EHS regulatory compliance management in the construction industry. These field-based solutions enable project managers and safety officers to conduct inspections, document incidents, and track compliance metrics directly from their mobile devices, significantly improving efficiency and accuracy.
Modern compliance apps feature intuitive interfaces that allow users to complete safety checklists, capture photo evidence, and generate instant reports on-site. Real-time data synchronization ensures that all stakeholders have immediate access to critical compliance information, enabling quick decision-making and prompt corrective actions when necessary.
Key features of these mobile solutions typically include:
– Digital forms and checklists customized to specific regulatory requirements
– GPS-enabled site tracking and documentation
– Automated notification systems for compliance deadlines
– Real-time incident reporting and investigation tools
– Cloud-based storage for easy access to historical compliance data
Remote monitoring capabilities have become particularly valuable, allowing safety managers to oversee multiple construction sites simultaneously. IoT sensors and wearable devices can track environmental conditions, equipment usage, and worker safety parameters, providing early warning signs of potential compliance issues.
For maximum effectiveness, these technologies should be integrated with existing project management systems and supported by comprehensive training programs. This ensures that all team members can effectively utilize these tools while maintaining focus on core safety objectives and regulatory requirements.
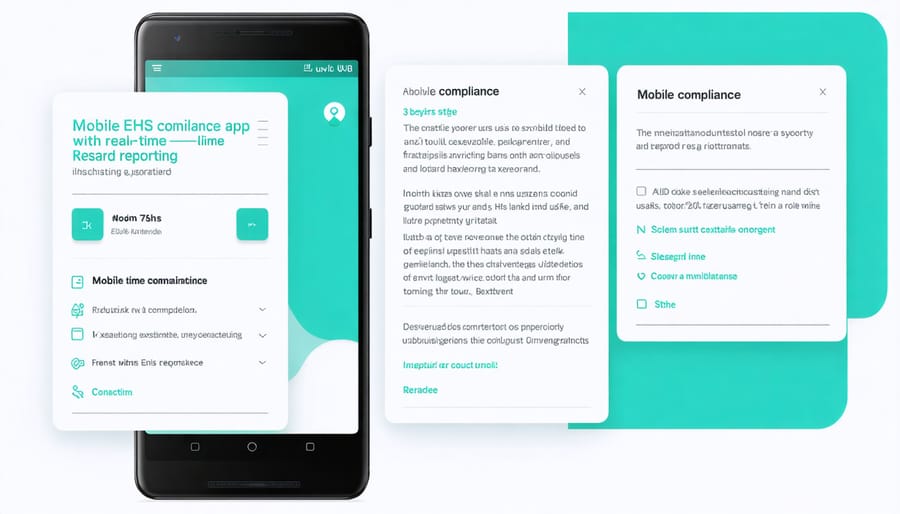
Common Compliance Challenges and Solutions
Case Studies and Best Practices
The success of EHS regulatory compliance often lies in learning from real-world implementations. A notable example is the Turner Construction Company’s comprehensive compliance program, which reduced workplace incidents by 45% over three years through systematic risk assessment and proactive safety measures. Their approach integrated digital monitoring systems with traditional QA/QC standards to ensure consistent compliance across multiple project sites.
Another instructive case study comes from Skanska USA, which implemented a mobile-first EHS reporting system across their operations. This initiative resulted in a 60% improvement in incident reporting time and a 30% increase in near-miss documentation, leading to better preventive measures. The key to their success was combining technology with comprehensive staff training and clear communication protocols.
The Port of Seattle’s Terminal 5 expansion project demonstrates best practices in environmental compliance management. The project team developed a innovative approach to handling contaminated soil and maintaining air quality standards while meeting strict regulatory requirements. Their method included real-time air quality monitoring and immediate response protocols, resulting in zero environmental violations throughout the three-year project duration.
Small to medium-sized contractors can learn from Hoffman Construction’s approach to compliance management. They created a scalable system that emphasizes regular training updates, clear documentation procedures, and integrated safety protocols. This systematic approach helped them maintain perfect compliance scores across multiple jurisdictions while reducing administrative overhead by 25%.
These cases highlight several common success factors:
– Integration of digital tools with traditional compliance methods
– Regular training and clear communication channels
– Proactive monitoring and reporting systems
– Documentation standardization
– Engagement of all stakeholders in the compliance process
– Continuous improvement based on data analysis
Effective EHS regulatory compliance remains a cornerstone of successful construction operations, demanding continuous attention and proactive management. By implementing comprehensive compliance programs, maintaining thorough documentation, and leveraging modern technology solutions, organizations can significantly reduce risks while fostering a culture of safety and responsibility. Regular training, systematic audits, and clear communication channels ensure that compliance measures remain current and effective. Remember that EHS compliance is not merely about meeting legal requirements—it’s about protecting workers, preserving the environment, and maintaining your organization’s reputation and operational efficiency. Success in this area requires unwavering commitment from leadership, active participation from all stakeholders, and a willingness to adapt to evolving regulatory landscapes. By staying ahead of compliance requirements and treating them as opportunities for improvement rather than obstacles, construction companies can build stronger, safer, and more sustainable operations for the future.