3D printing technology is revolutionizing the construction industry with unprecedented speed, precision, and cost-effectiveness. From printing entire residential structures in under 24 hours to fabricating complex architectural components on-demand, this disruptive technology is fundamentally transforming traditional building methodologies. Industry leaders are witnessing 40-60% reductions in construction time and up to 80% decrease in labor costs through strategic implementation of 3D printing solutions.
The implications extend far beyond mere efficiency gains. Construction firms leveraging advanced 3D printing systems are achieving previously impossible architectural designs, minimizing material waste by up to 30%, and dramatically reducing their carbon footprint. In 2023 alone, over 200 large-scale construction projects worldwide have successfully integrated 3D printing technology, marking a pivotal shift in how we approach modern building practices.
As construction costs continue to rise and skilled labor shortages persist, 3D printing emerges as a viable solution to these industry-wide challenges. This technology isn’t just an alternative to conventional methods – it’s becoming an essential tool for construction companies aiming to maintain competitiveness in an increasingly demanding market. The ability to rapidly prototype, iterate designs, and execute complex structures with precision is redefining what’s possible in construction.
The Evolution of Construction 3D Printing Technology
Current Capabilities and Limitations
Current construction 3D printing technology can produce structures up to four stories high with dimensional accuracy of ±0.5mm. Most systems utilize specialized concrete mixtures and can print walls, foundations, and basic structural elements at speeds of 100-150 square meters per day. The technology excels in creating complex geometrical shapes and curved surfaces that would be challenging with traditional construction methods.
However, significant limitations remain. Current systems typically require ideal weather conditions and can’t yet handle all building components – especially horizontal elements like floor slabs and roofs, which still need conventional construction methods. Material options are primarily limited to concrete-based mixtures, though research into alternative materials is ongoing. Reinforcement integration remains a challenge, with most solutions requiring manual placement of steel reinforcement between printed layers.
The technology also faces regulatory hurdles, as many jurisdictions lack specific building codes for 3D-printed structures. While suitable for basic structural elements, the process currently can’t handle complex mechanical, electrical, and plumbing installations, which must be integrated separately. Despite these constraints, rapid technological advancement suggests many current limitations will be overcome in the near future.

Material Innovation and Sustainability
The evolution of 3D printing materials has revolutionized construction sustainability, introducing innovative composites that align with modern sustainable design practices. Recent developments include bio-based materials derived from agricultural waste, recycled construction debris, and advanced polymer blends that significantly reduce carbon footprint while maintaining structural integrity.
Industry leaders have successfully implemented carbon-negative concrete alternatives, incorporating CO2-absorbing materials that sequester greenhouse gases during the printing process. These materials not only reduce environmental impact but also demonstrate superior durability and weather resistance compared to traditional construction materials.
The circular economy approach in 3D printing materials has gained substantial traction, with manufacturers developing processes to recycle and repurpose printed structures at the end of their lifecycle. This advancement addresses both waste reduction and resource conservation challenges facing the construction sector.
Emerging research focuses on self-healing materials and adaptive composites that can respond to environmental conditions, potentially extending building lifespans and reducing maintenance requirements. These innovations represent a significant step toward more resilient and environmentally responsible construction methods.
Market Impact and Cost Analysis
Project Timeline Reduction
The integration of 3D printing technology in construction has revolutionized traditional project timelines, emerging as one of the most game-changing building solutions in recent years. Analysis of completed projects reveals significant time reductions, with some developments reporting completion rates up to 60% faster than conventional construction methods.
Case studies from leading construction firms demonstrate that 3D printing can reduce a typical three-month building schedule to just four weeks. This acceleration stems from several key factors: automated continuous printing processes, reduced labor dependencies, and minimal material handling requirements. The technology eliminates numerous time-consuming traditional construction steps, such as formwork assembly and multiple trade coordination.
Project managers report particularly notable efficiency gains in foundation work and wall construction, where 3D printing can complete structures in days rather than weeks. The technology also minimizes weather-related delays, as printing can occur in controlled environments when necessary. Additionally, the precision of 3D printing significantly reduces rework time, with error rates dropping by up to 90% compared to traditional methods.
Real-time project data indicates that the greatest time savings occur during the actual construction phase, though some additional time may be required during the initial planning and design stages to optimize designs for 3D printing capabilities. This front-loaded planning ultimately contributes to smoother execution and fewer delays during construction.
Cost-Benefit Comparison
A comprehensive analysis of 3D printing versus traditional construction methods reveals significant cost variations across different project scales and types. Initial investment in 3D printing technology typically ranges from $150,000 to $1 million for industrial-grade equipment, representing a substantial upfront cost. However, operational savings typically offset this investment within 18-36 months through reduced labor costs and material efficiency.
Studies indicate that 3D-printed structures can reduce construction costs by 20-40% compared to conventional methods. Labor costs, which traditionally account for 40-60% of construction budgets, can be reduced by up to 80% through automation. Material waste reduction of 30-60% further contributes to cost savings, while shorter project timelines decrease overhead expenses and financing costs.
However, these benefits must be weighed against certain financial considerations. Specialized materials for 3D printing currently cost 10-15% more than traditional construction materials, though prices are expected to decrease as adoption increases. Maintenance and technical support for 3D printing systems add approximately 5-8% to annual operational costs.
The most favorable cost-benefit ratios are observed in projects with repetitive elements or complex geometries that would be expensive to construct traditionally. Small to medium-sized residential projects show ROI periods of 2-3 years, while larger commercial projects may see returns within 12-18 months, particularly when factoring in reduced construction time and earlier occupancy potential.
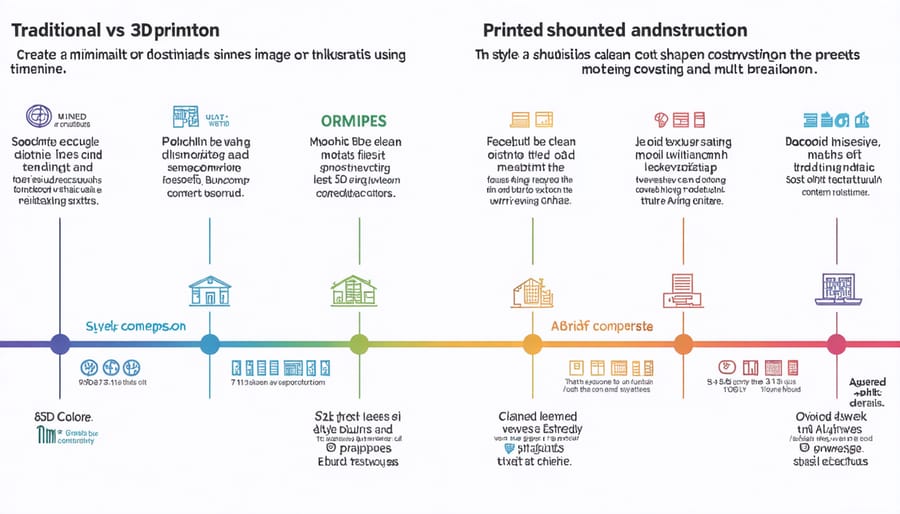
Real-World Applications and Case Studies
Commercial Building Projects
Commercial 3D printing projects are revolutionizing the construction industry, with several landmark developments showcasing the technology’s transformative potential. Leading construction firms are increasingly integrating 3D printing alongside traditional modular construction techniques to achieve unprecedented efficiency gains and cost reductions.
Recent projects demonstrate compelling outcomes, with completion times reduced by up to 60% compared to traditional methods. The 3D-printed office building in Dubai, completed in just 17 days, serves as a prime example of rapid deployment capabilities. Similarly, the Amsterdam Canal House project showcases how 3D printing enables complex architectural designs while maintaining structural integrity.
Cost analyses from completed projects indicate savings between 30-60% on labor expenses and a 20-25% reduction in material waste. These efficiencies are particularly evident in markets facing skilled labor shortages or high construction costs. Additionally, commercial projects utilizing 3D printing technology have reported enhanced sustainability metrics, with carbon footprint reductions of up to 40% compared to conventional construction methods.
The technology’s precision and repeatability have proven especially valuable for multi-story commercial structures, where standardized elements can be rapidly produced while maintaining strict quality controls.
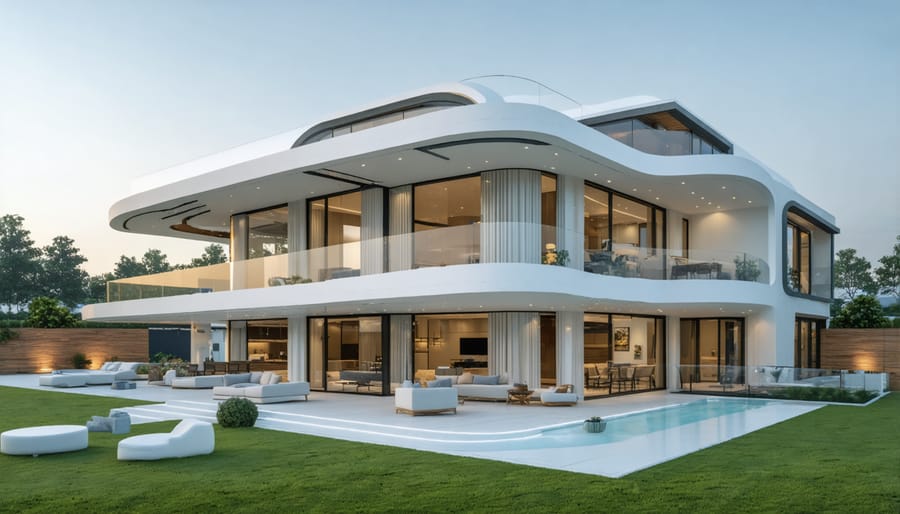
Residential Development Innovation
The residential construction sector has witnessed remarkable transformations through 3D printing technology, with several groundbreaking projects demonstrating its viability. ICON’s development in Mexico, creating a 50-home community for underprivileged families, showcased how 3D printing can address housing affordability while maintaining structural integrity. The project reduced construction time by 60% compared to traditional methods.
Market reception has been increasingly positive, with early adopters reporting 20-30% cost savings on overall project budgets. In Europe, Project Milestone in Eindhoven, Netherlands, successfully delivered the first commercially rental 3D-printed houses, garnering significant attention from both industry professionals and potential homeowners.
Recent surveys indicate that 68% of construction firms are now considering incorporating 3D printing technology into their residential development strategies. The technology’s ability to create custom designs without additional costs has particularly appealed to luxury home developers, while its efficiency in producing affordable housing units has attracted government housing authorities.
Key success factors include improved material formulations, refined printing processes, and better integration with existing construction workflows. Challenges remain in regulatory compliance and standardization, but early market performance suggests strong growth potential in residential applications.
Future Implications for the Construction Industry
The integration of 3D printing technology is rapidly reshaping construction’s future, with projections indicating transformative changes across multiple sectors. Industry analysts predict that by 2030, up to 30% of new commercial buildings could incorporate 3D-printed elements, dramatically reducing construction timelines and labor costs.
The emergence of hybrid construction methods, combining traditional techniques with additive manufacturing, is expected to become standard practice. This evolution will necessitate new skill sets among workforce members, with increased demand for digital design specialists and 3D printing technicians. Construction companies will need to invest in comprehensive training programs and update their operational frameworks to accommodate these technological advances.
Environmental considerations will drive further adoption, as 3D printing’s precise material usage can reduce waste by up to 40% compared to traditional methods. The technology’s capability to utilize recycled materials and sustainable composites will become increasingly important as environmental regulations tighten globally.
Supply chain dynamics will undergo significant transformation, with local manufacturing hubs potentially replacing traditional material distribution networks. This shift could reduce transportation costs and carbon emissions while improving project timeline predictability.
Looking ahead, regulatory frameworks will need to evolve to address quality control, safety standards, and certification processes for 3D-printed structures. Industry leaders are already collaborating with regulatory bodies to establish comprehensive guidelines that will facilitate wider adoption while ensuring structural integrity and safety compliance.
The technology’s scalability and customization capabilities suggest a future where mass-customization becomes economically viable, potentially revolutionizing both residential and commercial construction sectors.
3D printing technology has fundamentally transformed the construction industry, ushering in a new era of efficiency, sustainability, and innovation. As demonstrated throughout this analysis, the technology’s ability to reduce costs, minimize waste, and accelerate project timelines has proven invaluable across diverse construction applications. The integration of advanced materials, sophisticated design capabilities, and automated processes has positioned 3D printing as a cornerstone of modern construction methodology.
Looking ahead, the trajectory of 3D printing in construction appears increasingly promising. Industry experts project continued advancement in materials science, printing technologies, and automation systems, potentially enabling even larger-scale projects and more complex architectural designs. The growing emphasis on sustainable construction practices and the pressing need for affordable housing solutions worldwide will likely accelerate adoption rates among construction firms.
However, success in implementing this disruptive technology requires careful consideration of regulatory frameworks, workforce training, and quality control measures. As the technology matures, construction professionals must remain adaptable and forward-thinking, ready to embrace new possibilities while maintaining strict safety and quality standards. The future of construction undoubtedly lies in the strategic integration of 3D printing technology alongside traditional methods, creating a more efficient, sustainable, and innovative built environment.