HVAC building automation systems revolutionize modern facility management by integrating sophisticated control algorithms, sensor networks, and smart controllers to optimize building performance. These intelligent systems transform traditional heating, ventilation, and air conditioning operations into precisely orchestrated environments that respond dynamically to occupancy patterns, environmental conditions, and energy demands.
At its core, building automation represents the convergence of HVAC engineering and digital technology, enabling unprecedented levels of control over indoor environmental quality while significantly reducing energy consumption. Modern BAS platforms seamlessly coordinate multiple building systems – from air handlers and chillers to VAV boxes and thermostats – through a centralized management interface that provides real-time monitoring, automated scheduling, and predictive maintenance capabilities.
For facility managers and building owners, implementing HVAC automation delivers measurable returns through reduced operating costs, improved occupant comfort, and enhanced equipment longevity. The ability to fine-tune environmental parameters, detect system inefficiencies, and respond rapidly to changing conditions makes these systems indispensable in today’s high-performance buildings. Understanding how HVAC automation works is crucial for professionals seeking to optimize their facilities’ operations and achieve sustainable building management goals.
The Core Components of HVAC Building Automation
Sensors and Data Collection
Modern HVAC automation systems rely on a sophisticated network of sensors and data collection devices to maintain optimal building conditions. Temperature sensors are strategically placed throughout zones to monitor ambient conditions, while humidity sensors ensure proper moisture levels for occupant comfort and equipment protection.
Pressure sensors monitor air distribution across the system, detecting potential blockages or inefficiencies in ductwork. CO2 sensors measure indoor air quality and adjust ventilation rates based on occupancy levels, while occupancy sensors directly track space utilization to optimize conditioning schedules.
Advanced systems incorporate airflow sensors to monitor ventilation effectiveness and energy consumption. Integration of power monitoring sensors enables real-time tracking of equipment performance and energy usage patterns. Refrigerant pressure sensors ensure proper system operation and early detection of potential maintenance issues.
Data from these sensors is continuously collected and analyzed by the building automation system’s central controller. This information drives automated responses and helps facility managers make informed decisions about system optimization. Modern sensors often feature self-diagnostic capabilities and can communicate potential maintenance needs before system failures occur, enabling proactive maintenance strategies.
Central Control Systems
The central control system serves as the brain of HVAC building automation, comprising sophisticated management software and a primary control unit that oversees all system operations. This centralized platform typically features a user-friendly interface that enables facility managers to monitor, control, and optimize HVAC operations across multiple zones or entire buildings from a single dashboard.
Modern control systems utilize advanced algorithms and real-time data processing to make intelligent decisions about heating, cooling, and ventilation requirements. The management software integrates various subsystems, including temperature sensors, humidity monitors, and occupancy detectors, to maintain optimal environmental conditions while maximizing energy efficiency.
These systems often incorporate scheduling capabilities, allowing for automated adjustments based on building occupancy patterns and operational hours. The control unit continuously analyzes performance metrics, generating detailed reports and alerts for potential issues before they escalate into major problems. Remote access capabilities enable facility managers to monitor and adjust settings from anywhere, ensuring responsive building management even during off-hours or emergencies.
For enhanced reliability, many central control systems feature redundant processors and backup power supplies, guaranteeing uninterrupted HVAC operation during critical situations.
Smart HVAC Equipment Integration
Modern HVAC automation systems support integration with a wide range of smart equipment, including variable air volume (VAV) units, chillers, boilers, and air handling units (AHUs). These components communicate through standardized protocols such as BACnet, Modbus, and LonWorks, ensuring seamless interoperability across different manufacturers and systems. Advanced controllers and sensors enable real-time monitoring and adjustment of temperature, humidity, and air quality parameters. Direct digital control (DDC) systems serve as the backbone, allowing precise manipulation of mechanical equipment through programmable logic controllers. The integration extends to supporting systems like variable frequency drives (VFDs) for fans and pumps, smart thermostats, and occupancy sensors, creating a cohesive network that optimizes energy efficiency and operational performance.
Energy Efficiency and Cost Benefits
HVAC building automation systems represent a significant advancement in modern facility management, delivering substantial energy savings and cost reductions through intelligent control and optimization. Studies show that properly implemented automation systems can reduce HVAC-related energy consumption by 20-30%, with some AI-powered building systems achieving even higher efficiency gains.
The cost benefits materialize through multiple channels. First, automated systems optimize HVAC operation schedules based on actual building occupancy patterns, preventing unnecessary heating or cooling of unused spaces. Advanced sensors and controls maintain precise temperature and humidity levels, eliminating energy waste from overcooling or overheating.
Predictive maintenance capabilities significantly reduce operational costs by identifying potential equipment issues before they lead to failures or increased energy consumption. This proactive approach extends equipment lifespan and minimizes emergency repair expenses, contributing to lower total ownership costs.
Real-time monitoring and adjustment capabilities ensure that HVAC systems operate at peak efficiency throughout varying conditions. For example, automated systems can adjust operation based on weather forecasts, occupancy levels, and time-of-use utility rates, maximizing cost savings while maintaining comfort levels.
Implementation of energy-efficient building solutions through automation typically delivers ROI within 2-3 years. Case studies from commercial buildings show annual energy cost reductions of 25-35%, with some facilities reporting payback periods as short as 18 months.
These systems also contribute to demand-side management programs, allowing facilities to participate in utility incentives and rebate programs. By automatically adjusting HVAC operations during peak demand periods, buildings can benefit from reduced utility rates while maintaining essential comfort levels.
Furthermore, automated systems provide detailed energy consumption data and analytics, enabling facility managers to identify additional optimization opportunities and validate energy-saving initiatives. This data-driven approach ensures continuous improvement in energy efficiency and cost reduction strategies over time.
Real-Time Monitoring and Predictive Maintenance
Real-time monitoring and predictive maintenance capabilities represent the cornerstone of modern HVAC building automation systems, enabling facilities managers to optimize system performance while minimizing downtime. These sophisticated systems utilize an array of sensors and data analytics to continuously monitor critical parameters including temperature, humidity, pressure, airflow, and equipment performance metrics.
Advanced analytics platforms process this continuous stream of data to establish baseline performance patterns and identify potential issues before they escalate into system failures. By analyzing historical performance data alongside real-time metrics, these systems can detect subtle variations that might indicate developing problems, such as bearing wear, reduced cooling efficiency, or impending component failure.
The predictive maintenance approach leverages machine learning algorithms to forecast when equipment maintenance will be required, moving beyond traditional schedule-based maintenance to a more efficient condition-based model. This proactive strategy typically reduces maintenance costs by 20-30% while extending equipment life span by up to 25%.
Key monitoring capabilities include:
– Real-time performance tracking and optimization
– Energy consumption analysis and trending
– Equipment runtime monitoring
– Fault detection and diagnostics
– Automated maintenance scheduling
– Performance degradation analysis
When anomalies are detected, the system automatically generates alerts and work orders, prioritizing maintenance tasks based on urgency and potential impact. This automated approach ensures that maintenance resources are allocated efficiently, focusing on equipment that truly requires attention rather than conducting unnecessary routine checks.
The integration of mobile applications allows maintenance teams to receive instant notifications and access detailed diagnostic information from anywhere in the facility. Technicians can view equipment histories, access maintenance procedures, and update work orders in real-time, significantly improving response times and maintenance efficiency.
Through comprehensive data collection and analysis, these systems also provide valuable insights for long-term planning and capital investment decisions, helping facility managers make informed choices about equipment replacement and system upgrades based on actual performance data and lifecycle cost analysis.
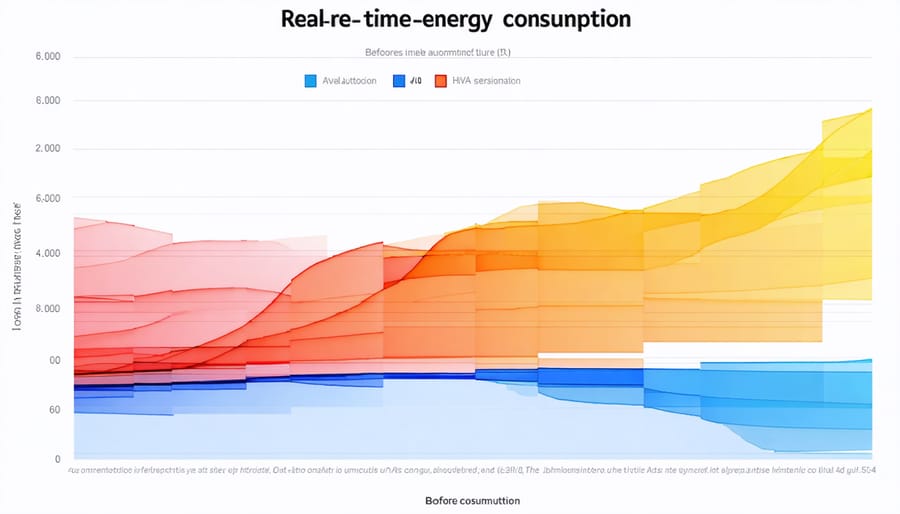
Integration with Smart Building Systems
Building Management Systems (BMS)
Building Management Systems (BMS) serve as the central nervous system of modern building operations, orchestrating various subsystems including HVAC automation. These integrated platforms coordinate multiple building functions through a unified interface, enabling seamless operation and enhanced efficiency. By incorporating smart energy management systems, BMS solutions optimize resource utilization while maintaining optimal indoor environmental conditions.
The integration capabilities of modern BMS platforms extend beyond basic HVAC control, encompassing lighting, security, fire safety, and access control systems. This comprehensive approach allows facility managers to monitor and adjust building operations in real-time through sophisticated dashboards and control interfaces. The system’s ability to collect and analyze data from multiple sources enables predictive maintenance strategies and performance optimization.
Key features of BMS integration include automated scheduling, fault detection and diagnostics, energy consumption tracking, and occupancy-based control algorithms. These systems can adapt to changing conditions through advanced sensors and controllers, maintaining comfort levels while minimizing energy waste. The coordination between different building systems ensures efficient operation during both peak usage periods and off-hours, contributing to significant cost savings and improved occupant satisfaction.
Modern BMS platforms also support remote monitoring and control capabilities, allowing facility managers to oversee operations from anywhere while maintaining secure system access. This flexibility has become increasingly important for maintaining building operations during unexpected circumstances or reduced staffing situations.
IoT and Cloud Connectivity
Modern HVAC building automation systems leverage advanced IoT and cloud technologies to deliver unprecedented control and efficiency. IoT integration in smart buildings enables real-time monitoring, predictive maintenance, and dynamic system adjustments through secure cloud platforms.
Connected sensors throughout the building continuously collect data on temperature, humidity, occupancy, and air quality. This information is transmitted to cloud servers where sophisticated algorithms analyze patterns and optimize system performance. Facility managers can access this data and control systems remotely through secured web portals or mobile applications, enabling immediate response to environmental changes or maintenance needs.
Cloud connectivity also facilitates integration with other building systems, creating a cohesive building management ecosystem. Weather forecasts, energy pricing data, and occupancy schedules can automatically influence HVAC operations, maximizing both comfort and efficiency. The system can proactively adjust settings based on predicted conditions rather than merely reacting to current situations.
Advanced cybersecurity protocols protect these connected systems from unauthorized access while ensuring reliable communication between components. Regular over-the-air updates keep the system current with the latest features and security patches, extending the lifetime value of the installation. This connectivity infrastructure forms the backbone of modern building automation, enabling smart decisions based on comprehensive data analysis and real-time environmental conditions.
Implementation Considerations
Successful implementation of HVAC building automation systems requires careful planning and consideration of several key factors. First, conduct a thorough assessment of your existing HVAC infrastructure and building requirements. This evaluation should include current energy consumption patterns, occupancy schedules, and specific comfort needs across different zones.
Select automation components that are compatible with your existing systems and scalable for future expansion. Consider open-protocol solutions that enable integration with other building systems and third-party devices. Leading protocols like BACnet, Modbus, and LonWorks offer flexibility and interoperability across different manufacturers.
Establish a phased implementation approach to minimize disruption to building operations. Begin with core functionalities like basic scheduling and temperature control before advancing to more sophisticated features such as predictive maintenance and AI-driven optimization.
Ensure proper sensor placement throughout the building for accurate data collection. Strategic positioning of temperature, humidity, and occupancy sensors is crucial for system effectiveness. Install sensors away from direct sunlight, air vents, and heat-generating equipment to obtain reliable readings.
Invest in comprehensive staff training to maximize system benefits. Facility managers and maintenance personnel should understand both daily operations and troubleshooting procedures. Regular training updates help teams adapt to system upgrades and new features.
Implement robust cybersecurity measures to protect your automation system. This includes secure network configurations, regular software updates, and access control protocols. Document all system modifications and maintain detailed operational procedures for long-term success.
Create a preventive maintenance schedule that aligns with manufacturer recommendations and building usage patterns. Regular system audits help identify optimization opportunities and ensure continued efficiency.
HVAC building automation systems represent a critical investment in the future of construction and facility management. By integrating smart controls, sensors, and advanced analytics, these systems deliver substantial energy savings, improved occupant comfort, and reduced operational costs. The ROI continues to strengthen as technology advances, with modern systems offering predictive maintenance capabilities and seamless integration with other building systems. Looking ahead, the industry is moving toward AI-driven optimization, cloud-based management, and even greater interoperability between different manufacturers’ systems. As sustainability requirements become more stringent and energy costs rise, HVAC automation will play an increasingly vital role in meeting both regulatory compliance and operational efficiency goals. For construction professionals and building owners, implementing these systems is no longer optional but essential for maintaining competitive advantage in today’s smart building landscape.